Adhesive-joint-design
for uniform successful stressing.
SOLUTIONS with Effective, Practical Advice
Clever Adhesive-joint-design considers special
advantages
and limitations of this class of joining processes.
It also takes into account joining
best practices.
These are a most important factor for the successful application of
Structural Adhesion Bonding.
In a previous page on Adhesive Bonding, including also Advantages and Limitations, we introduced this important group of processes.
It is uniquely suited to provide effective joining solution when the adhesive system characteristics are exploited.
Also when all manufacturing requirements and safety provisions are duly accounted for.
In this new page we intend to concentrate on Adhesive-joint-design.
Adhesive-joint-design considerations
The first and foremost consideration for Adhesive-joint-design is to scrutinize the adhesion types of stress felt by the adhesive bonded joint.
The stressing mode to prefer in Adhesive-joint-design is that involving shear stress, stressing along the plane of the joint.
This is the most effective mode of stressing where the properties of the bonding material, the adhesive, are used to their best capability.
If you did not yet find what you need, why not typing your question in the following Search Box?
The importance of good Adhesive-joint-design for load carrying capability of Adhesive bonded joints cannot be overstated.
The outstanding advantage of an adhesive joint is that stresses are distributed relatively more uniformly throughout the joint than with other localized methods (spot welding, riveting, bolting etc.).
Adhesive bonded joints however do not present absolute uniform loading as stresses concentrate at the borders of the joint.
The main reason why one has to reckon also other less favorable stressing conditions in Adhesive-joint-design, is that only seldom the load types give rise to a well defined and pure shear stress in the adhesive bonded joint.
In most of practical cases there will be a mixed stress situation where also less favorable tensile, cleavage and peel stresses will be active as follows:
- Tensile stress, directed normal (orthogonal, at 90 degrees) to the joint plane
- Cleavage stress, concentrated at one edge and trying to rotate one element relative to the other
- Peel stress, concentrated along a very narrow line at the edge of the bond area and gradually separating one bonded element from the adhesive joint
An interesting mixed solution (also called Hybrid Joining) designed to avoid the peel stress in the adhesive consists in fixing the free end of the joint by means of a mechanical fastener (rivet or bolt-nut) or of a resistance spot weld.
Torsion stress that operates between adhesive bonded concentric elements transmitting or resisting torque is similar in behavior to shear stress. Another torsion stress may exist between two elements adhesive bonded across a plane area if a rotary moment is active, stressing the joint in torsion.
Compression stress is not dangerous to the integrity of the joint in that it does not try to separate the elements from one another.
When considering upgrading of a joint originally designed for welding, one cannot, in general, substitute the application of a structural adhesive for whatever process was used before. One should instead take advantage of the special properties of adhesives, and beware of their limitations.
Once determined the joint type, one has to establish the actual design dimensions and tolerances. In particular the gap has an important influence on strength and should be carefully selected. In general a thin adhesive layer is preferred.
A decrease in the apparent shear strength is reported as the bond line thickness is increased. It is so qualified (apparent) because it was found to be highly dependent on the adherend bending stiffness, which directly affects the peel stress distributions in the adhesive layer.
In a study of the single lap joint described in the ASTM D1002 testing procedure it was found that due to the material elastic mismatch and the eccentricity of the test setup, a mixed mode loading is introduced to the adhesive joint. Therefore it is doubtful if results from this test can be used as Adhesive-joint-design criteria.
Of the properties of adhesive and adherends likely to influence the stress condition in the joint one should consider:
- Mismatch between Coefficient of Thermal Expansion (CTE) of the adhesive relative to the materials joined (the adherends). In case of good match, internal stresses will be minimal, otherwise they may be substantial.
- A low modulus of elasticity of the adhesive makes it compliant, producing low stress. A rigid adhesive (with high modulus) will display high internal stress.
- Flexibility and toughness in the adhesive are desired for long time endurance. Rigid and inflexible adhesive may be prone to cracking and failure.
For standard applications of commercial adhesives the following Adhesive-joint-design guidelines are proposed, besides the already recommended stressing of the adhesive joint in shear and avoiding as much as possible peel and cleavage stresses :
- Stiffer adherend, relative to the adhesive, provides more uniformly distributed stress in the joint, and higher bond strength.
- Shear stress is better resisted by stiff adhesives.
To resist peel stress flexible and tough adhesives are preferable.
- Stronger joints and lower deformation result from higher product of adherend modulus per its thickness.
Furthermore manufacturing practice should promote uniform, void free adhesive joint.
Accepted testing standards for Adhesive-bonding joints are:
ASTM D1002-10
Standard Test Method for Apparent Shear Strength of Single-Lap-Joint Adhesively Bonded Metal Specimens by Tension Loading (Metal-to-Metal)
ASTM International / 01-Oct-2010 / 6 pages
ASTM D1876-08
Standard Test Method for Peel Resistance of Adhesives (T-Peel Test)
ASTM International / 01-Oct-2008 / 3 pages
Adhesive Manufacturers use to publish typical data of their products referring to these standard tests.
See also the following:
Adhesive Joints - Design and Calculation
http://www.eaa.net/eaa/education/TALAT/lectures/4703.pdf
TWI - Adhesive bonding - a guide to best practice
Section 3. Joint design, plus adhesive bonding case-histories
http://www.twi.co.uk/j32k/protected/band_10/bpads03.html
(may need no cost registration) (Removed by TWI)
Adhesive Tool Kit
http://www.adhesivestoolkit.com/Toolkits.xtp
For a thorough study of all aspects of Adhesive Joining and Adhesive-joint-design you may wish to consider investing in the fundamental book on Adhesive Bonding
Conclusion
Although Adhesive-joint-design has enjoyed successful applications in many industries, including aerospace, marine, automotive and transportation, especially because of its potential to reduce weight of joints, there is a widespread hesitation to implement complete transition to structural adhesive bonding.
Replacing traditional fasteners in primary structural applications by structural adhesive bonding would require a more thorough understanding of bonded joint performance over the life of a structure, including properties like overall joint toughness, creep, and fatigue.
Furthermore, despite huge progress, there is still lack of confidence in the ability to control all adhesive application manufacturing variables, to the extent needed for validation of adhesive bonded systems capability to meet service requirements for these structures in the total absence of mechanical fasteners.
Therefore development will probably take the time needed to obtain more and better research results and to accumulate richer experience.
Only then bolder application will slowly be introduced until primary structural adhesive joints will become commonplace although produced through highly demanding requirements and manufactured by specialized facilities.
An Article on Testing Automotive Composites was published (3) in Issue 152 of Practical Welding Letter for April 2016.
Click on PWL#152.
* * *
If you are not opposed to view a commercial Video (No Endorsement or Promotion intended) on
Preparing adhesive joints and troubleshooting
You may wish to watch the following:
https://www.youtube.com/watch?v=YhougI1f-Qw
|
* * *

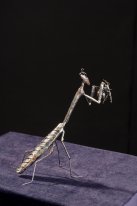
Insect
[From https://www.welding-advisers.com/nature.html]
Any questions or comments or feedback? Write them down and send them to us by e-mail.
Click on the Contact Us button in the NavBar at top left of every page.
Let us remind you that, if you are interested, we offer a no cost subscription to our Practical Welding Letter and a bonus book in pdf format to be made available for download to your computer on the subject of
PRACTICAL HARDNESS TESTING MADE SIMPLE. Click on Subscription.
To reach a Guide to the collection of the most important Articles from Past Issues of Practical Welding Letter, click on Welding Topics.
Back Home
Processes
Site Map
Adhesive Bonding
Forge Welding
Hot Pressure Welding
Roll Welding
Thermite Welding
Oxyacetylene Welding Tips
Vertical Welding Tips
Resistance Welding Tips
Pipe and Tube Welding
Welding Underwater Processes
Adhesive-joint-design Top
How could SBI! help you Retire
to useful and enjoyable life?
Watch the following Video...
Click on the following image to watch the SBI! TV Show!
POWERED BY:
Click on this Logo NOW!
Copyright (©) 2008, 2009, 2010, 2011, 2012, 2013, 2014, 2015, 2016, 2017
by Elia E. Levi and www.welding-advisers.com
All Rights Reserved
Adhesive-joint-design is a complex and difficult discipline. To achieve success, specialized help should be sought from Institutes or individuals of proven competence and experience.