Resistance-welding-tips
useful Hints and References.
SOLUTIONS with Effective, Practical Advice
Welding Problem? Solve it! with
Help from a Welding Professional Contact Us.
|
Note: To view Google Ads, Pls.
Right Click and Open in a New Window.
|
Resistance-welding-tips may have two meanings.
One is the electrode end, that in this case, in resistance welding, transmits compressive force and electric current to the item to weld.
The other one, to which we are devoting this page, refers to suggestions that may be helpful to anyone engaging in this type of process.
We dealt with this process in two previous pages, Resistance Welding Processes and Resistance Welding Equipment.
Now we want to present additional details and Resistance-welding-tips not addressed adequately till now, that influence setup and conduct of welding.
Classic application of resistance spot welding refers to overlapping joints of the same material and of the same thickness. In such case the electrode Resistance-welding-tips are identical in material, shape and dimensions resulting in heat balanced distribution and in a central spot welded nugget located symmetrically at the interface.
If the thickness of the elements and/or the thermal conductivity of the materials are different, the distribution of the current and of heat build up may be non symmetric, causing the nugget to be lop-sided and possibly unacceptable.
One or more of the following Resistance-welding-tips can be applied to redress the situation. An electrode tip with a smaller face area can be used from the side of the higher conductivity alloy or of the thinner sheet. Otherwise an electrode of higher electrical resistance (e.g. tungsten) may face the higher conductivity material. Such provisions will shift the current density and the heat distribution.
When using sets of different electrodes, proper controls must be established by design to avoid their erroneous misapplication.
Electrode tip faces are progressively deteriorating with use. To assure continuing high quality production it is imperative to follow Resistance-welding-tips that require to check periodically and to dress again their surface after the prescribed number of spot welds has been performed. In automated systems rigid schedules of electrode maintenance should be established.
Depending on the configuration of the parts to be welded, electrode Resistance-welding-tips of various shape and dimensions are available, mostly available as shelf items from suppliers of equipment and accessories as advertised in their catalogs.
Special bent tips may be needed to reach difficult spots but should never be used when the work can be done with standard cylindrical electrodes. Of the various Resistance-welding-tips one should remember that cooling water direction should be checked to make sure that the central cool water jet impinges on the internal back side of the electrode tip closest to the weld face to ensure maximum effective cooling.
Note: To view Google Ads, Please
Right Click and Open in a New Window.
|
While troubleshooting for spot weld problems one should pay attention mostly to two areas. One is the constant good condition of the electrode Resistance-welding-tips, that play a major ask in providing good welds. That is why severe maintenance schedules must be introduced and enforced.
The second is the good setup of adequate modern control devices, which may need updating and improvement, especially if weld results are not consistent.
Portable spot welding machines may be required to perform spot welding on large and cumbersome objects that cannot be readily brought to a standing welding machine. They are usually held by a structure that bears the weight and eases manual manipulation.
While the machine carries the electrodes and the force application mechanisms to deploy the necessary compressive force, the required power source can be either separate or integral with the unit.
In the first case electrical cables are connected to fixed transformers. Because of large power losses due to the cables, a higher secondary voltage is needed than in a stationary machine of the same current output.
In the second case as recommended by Resistance-welding-tips the transformer is integral with the portable unit which is called a "transgun", with the advantage that there is no voltage drop on the secondary cable. Although this configuration is used in manual units it can be easily mounted on robotic arms, especially after the adoption of Inverter technology since such transformers became much smaller and lighter.
The introduction of Insulated Gate Bipolar Transistors (IGBT) for MFDC, and the increased use of Silicon Controlled Rectifiers (SCR) permit fine adjustment of the amount of energy flowing to the transformer. Resistance-welding-tips suggest that modern control devices based on feedback should be employed to permit supply of constant direct current to each weld, even in cases of primary alternating current (AC) line voltage fluctuations.
The other necessary functions are easily regulated with standard equipment. Resistance-welding-tips recommend to use the latest technological developments available for feedback based process control. Force gauges are currently used for monitoring and controlling the applied force. Time control functions are now based on microprocessor digital technology. Obtaining consistently high quality welds is nowadays a much easier task than it was only a few decades ago.
Plated and coated steel sheets can be joined by resistance welding, following recommended Resistance-welding-tips. Welding procedures and schedules should preserve the coating presence and function, while providing welds of acceptable strength. Machine settings remain quite similar to those used on bare steel of similar thickness, but adjustments are required.
Compensation of coating type and thickness on contact resistance, effects on indentation, alloying of coating with electrode Resistance-welding-tips material, and coating pick-up should be cared for. Coating thickness and uniformity is most important, for good weldability the thinnest the better.
Resistance-welding-tips of coated steel call for higher welding current, greater electrode force and shorter welding time that that used for uncoated steel of same thickness. Good tip maintenance and effective electrode cooling are the best preventive actions.
The application of Medium Frequency Direct Current (MFDC) Power Sources was briefly reviewed in an article published (2) in Issue 42 of Practical Welding Letter for February 2007.
Click on PWL#042 to see it.
An Article on Consumable Process Tape for Spot Welding was published (4) in Issue 77 of Practical Welding Letter for January 2010.
Click on PWL#077 to read it.
A clarifying contribution on Spot Welding Duplex Stainless was reported (11) in issue 81 of Practical Welding Letter for May 2010.
Click on PWL#081 to see it.
An Article on Proper Water Cooling of Spot Welding Electrodes was published (3) in Issue 87 of Practical Welding Letter for November 2010.
Click on PWL#087 to see it.
An Article on Automated tip dressing for robotic Resistance Spot Welding was published (7) in issue 94 of Practical Welding Letter for June 2011. Click on PWL#094 to see it.
An Article on Establishing Squeeze Time was published (3) in issue 102 of Practical Welding Letter for February 2012.
Click on PWL#102 to read it.
An Article on Destructive Testing of Spot Welded Specimens was published (2) in Issue 103 of Practical Welding Letter for March 2012.
Click on PWL#103 to see it.
An Article on Spot Weld Lobes was published (2) in Issue 104 of Practical Welding Letter for April 2012.
Click on PWL#104 to see it.
A special Issue of Practical Welding Letter, the Mid June Bulletin No.74, full of Resources on Resistance Welding was published on June 14, 2012.
Click on PWL#106B to see it.
An Article on Strength of Stainless Spot Welds was published (11) in Issue 112 of Practical Welding Letter for December 2012.
Click on PWL#112 to see it.
An Article on Inserted strips in Resistance Spot Welding was published (3) in Issue 136 of Practical Welding Letter for December 2014.
Click on PWL#136 to see it.
Articles on Capacitor Discharge Welding (2) and Adaptive Controls for Resistance Seam Welders (7) were published in Issue 139 of Practical Welding Letter for March 2015.
Click on PWL#139 to see them.
An Article on Resistance Projection Welding Revisited was published (3) in Issue 150 of Practical Welding Letter for February 2016.
Click on PWL#150.
An Article on Follow-up on VFAW was published (2) in Issue 151 of Practical Welding Letter for March 2016.
Click on PWL#151.
An Article on Overview of modern Materials Testing Systems was published (7) in Issue 153 of Practical Welding Letter for May 2016.
Click on PWL#153.
An Article on Certified Resistance Welding Technician was published (3) in Issue 154 of Practical Welding Letter for June 2016.
Click on PWL#154.
An Article on Resistance Welding Tips was published (3) in Issue 156 of Practical Welding Letter for August 2016.
Click on PWL#156.
An Article on Update on VFAW was published (7) in Issue 159 of Practical Welding Letter for November 2016.
Click on PWL#159.
An Article on Low Impedance Resistance Welding was published (11) in Issue 162 of Practical Welding Letter for February 2017.
Click on PWL#162.
An Article on Resistance Spot Welding of Ultra-Thin Steel was published (2) in Issue 163 of Practical Welding Letter for March 2017.
Click on PWL#163.
An Article on Resistance Welding Nuts to High-Strength Low Alloy (HSLA) Steel was published (4) in Issue 168 of Practical Welding Letter for August 2017.
Click on PWL#168.
Get at no cost all the issues of Practical Welding Letter as they are published. Please subscribe.
You will also get the book "PRACTICAL HARDNESS TESTING MADE SIMPLE", see further down this page.
A Q&A note published at page 16 in the July 2011 of the Welding Journal, provides useful Resistance-welding-tips on the extension of time between dressing electrodes used for welding galvanized steel sheets. Besides stressing the role of efficient electrodes water cooling, the note introduces two new concepts.
The first is a special Heat/Cool/Weld Schedule that, although somewhat explained, will leave readers baffled when trying to realize it in practice for themselves.
The second is a commercial device, called Heat Stepper, designed to increase gradually the welding current with the number of spot welds, to compensate for area increase and contamination, providing up to 3000 acceptable spot welds between electrode dressing.
Although this is a commercial product that we do not endorse nor recommend, interested readers might want to check it for themselves and see if it is likely to improve their productivity.
Readers are urged to read that note, and possibly to contact the author, if they think that it may help them.
Resources
The following short list may be used as a Guide to find further information and overcome problems in need of troubleshooting.
Overview of Resistance Welding (10 pages)
http://www.livco.com/UMchapter1.pdf
Handbook for Resistance Spot Welding (20 pages)
http://www.millerwelds.com/pdf/Resistance.pdf
Understanding Control Modes in Resistance Welding
Article.
Testing Resistance Welding Transformers
http://www.geschmidt.com/technical/TestingTransformers.pdf
A few important AWS Resources, including Specifications and Recommended Practices, are available for purchase:
AWS A10.1M-2007
Specification for Calibration and Performance Testing of Secondary Current Sensing Coils and Weld Current Monitors used in Single-Phase AC Resistance Welding
American Welding Society / 05-Mar-2007 / 56 pages
ANSI/AWS C1.1M/C1.1:2000 (R2012)
Recommended Practices for Resistance Welding
American Welding Society / 01-Jan-2000 / 105 pages
ANSI/AWS C1.4M/C1.4:2009
Specification for Resistance Welding of Carbon and Low-Alloy Steels
Edition: 2nd
American Welding Society / 22-Aug-2008 / 32 pages
ANSI/AWS D8.1M:2007
Specification for Automotive Weld Quality - Resistance Spot Welding of Steel
Edition: 1st
American Welding Society / 12-Jan-2007 / 40 pages
ANSI/AWS D8.6:2005
Standard for Automotive Resistance Spot Welding Electrodes
American Welding Society / 20-Sep-2005 / 100 pages
ANSI/AWS D8.7M:2005
Recommended Practices for Automotive Weld Quality-Resistance Spot Welding
American Welding Society / 09-Dec-2004 / 30 pages
ANSI/AWS D8.9M:2012
Recommended Practices for Test Methods for Evaluating the Resistance Spot Welding Behavior of Automotive Sheet Steel Materials
American Welding Society / 22-Feb-2012 / 126 pages
ANSI/AWS D17.2-D17.2M-2007
Specification for Resistance Welding for Aerospace Applications
American Welding Society / 04-Jan-2007 / 44 pages
Watch the following Video on
Resistance Spot Welding - How It Works https://www.youtube.com/watch?v=AwL1CAg43PU
|
* * *
Any questions or comments or feedback? Write them down and send them to us by e-mail.
Click on the Contact Us button in the NavBar at top left of every page.
* * *
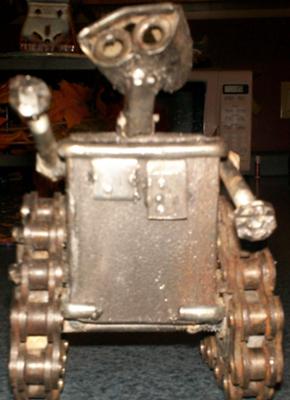
WALL-E
[From https://www.welding-advisers.com/the-wolfwolf-studio.html]
Let us remind you that, if you are interested, we offer a no cost subscription to our Practical Welding Letter and a bonus book in pdf format to be made available for download to your computer on the subject of
PRACTICAL HARDNESS TESTING MADE SIMPLE. Click on Subscription.
To reach a Guide to the collection of the most important Articles from Past Issues of Practical Welding Letter, click on Welding Topics.
Note: To view Google Ads, Please
Right Click and Open in a New Window.
|
Back Home
Processes
Site Map
Tig Welding Tips
Mig Welding Tips
Plasma Welding Tips
Flux Cored Arc Welding Tips
Submerged Arc Welding Tips
Shielded Metal Arc Welding Tips
Oxyacetylene Welding Tips
Vertical Welding Tips
Pipe and Tube Welding
Welding Underwater Processes
Brazing
Brazing Joint Design
Brazing Heating
Braze Welding
Resistance Brazing
Soldering
Wave Soldering
If you did not yet find what you need, why not typing your question in the following Search Box?
Resistance-welding-tips Top
Watch the following Video...
Click on the following image to watch the SBI! TV Show!
POWERED BY:
Click on this Logo NOW!
Watch - The Video:
Why Don't I Work From Home?
and also
Think outside the Cube.
Follow this Invitation!
Experience C2 power and flexibility in action by clicking SBI! 2.0 For You. Where SBIers share their business-building experiences first-hand. You will realize that there is nothing comparable to SBI! when you read real stories from SBIers who share how C2 has helped them expand, accelerate, build trust and monetize their sites.
|
Copyright (©) 2008, 2009, 2010, 2011, 2012, 2013, 2014, 2015, 2016, 2017
by Elia E. Levi and www.welding-advisers.com
All Rights Reserved