Beam-processing:
new applications for clever tools.
SOLUTIONS with Effective, Powerful Advice
Beam Processing Improves Performance
|
Beam-processing includes different applications using the already known high energy density beams utilized for successful welding, cutting or drilling.
See
High Energy Welding Processes,
Electron Beam Welding Tips,
High Energy Equipment,
Hybrid Welding,
Laser Drilling,
Laser Beam Welding,
Near Net Shape.
In this page, a few different uses of the powerful beams are reviewed, for Beam-processing metals without melting. When suitable equipment is available, such processing may have specific advantages if compared to traditional means for accomplishing equivalent operations.
Among other suitable processes, surface Heat Treating stands out as quite important, because it can be performed with this kind of equipment in a neat, clean, precise and economic way. This process can provide a hard case on selected spots, without heating the whole part.
It should be remembered that both the electron-beam and the laser beam can be manipulated, so that defocusing or rastering, rapid succession of parallel beam lines can be painted on the part, rapidly heating different areas in the proper sequence.
Beam-processing for special requirements
The EB vacuum environment is ideal for avoiding surface attack. When using laser beam it is not difficult to provide a local envelope of protective atmosphere.
High carbon steels, tool steels and martensitic stainless steels are quickly heated locally to the required transformation temperature, while the metal mass provides instant self quenching for developing the required martensitic hard structure.
Tempering can be performed in place with lower current heating or, if preferable, as an additional separated process with regular equipment.
Also stress relieving or Post Weld Heat Treatment can be performed after beam welding where required, by applying limited heating to those surfaces.
Another form of Beam-processing is available for inducing residual tensile stresses in selected portions of the parts, for providing a more favorable stress distribution.
A disc spinning under a definite area of rastered beams collects heat, at lower than melting temperature, concentrated in a zone limited by an external and an internal circumference.
Heated material tends to expand but is restrained by the cooler material surrounding it. It yields upon expansion. After cooling, this ring is under residual tensile stresses, (but the whole disc results prestressed in compression) likely to improve the performance of the disc in service.
In practice this application would leave a residual stress pattern similar to that left by a specific welding sequence depositing weld beads of definite shape and mass.
Prestressing discs along their circumference may improve their resistance to shattering, if they are subjected to centrifugal forces in service.
The abstract of an article on
Measuring residual stresses in metallic discs hardened on localized circular areas is available at:
Journal of Physics.
Local application of heat induces residual stresses that, if properly planned, can help straightening thermally warped parts.
Surface modification can be obtained by Beam-processing surfaces, covered with suitable materials in powder form, as the powder is locally fused and embedded in the base metal.
The EB vacuum though may disturb and remove the powder before it melts. Therefore low vacuum EB or laser beam applications may be preferred in these circumstances.
Deep penetration brazing is a specialized application of Beam-processing, mentioned in a paper at http://eagar.mit.edu/EagarPapers/Eagar134.pdf
Beam-processing is also widely applied for obtaining curing or definite properties improvements, in non metals or plastic parts, in solid state.
An Article introducing Additive Manufacturing and Resources was published (8) in Issue 146 of Practical Welding Letter for October 2015.
Click on PWL#146.
An Article on ENHANCED DIAMOND-LIKE COATINGS BOOST FUEL EFFICIENCY (A new laser arc method is being used to apply a hard carbon coating to engine components on the production line)
is reported (11) from iTSSe Nov/Dec 2015 in Issue 148 of Practical Welding Letter for December 2015.
Click on PWL#148.
An Article on Laser Surface Patterning Pre-Treatment was published (11) in Issue 151 of Practical Welding Letter for March 2016.
Click on PWL#151.
If you did not yet find what you need, why not typing your question in the following Search Box?
* * *
Watch the following
Laser Processing Video
https://www.youtube.com/watch?v=5MWdghmr7c8
* * *
Any questions or comments or feedback? Write them down and send them to us by e-mail. Click on the Contact Us button in the NavBar at top left of every page.
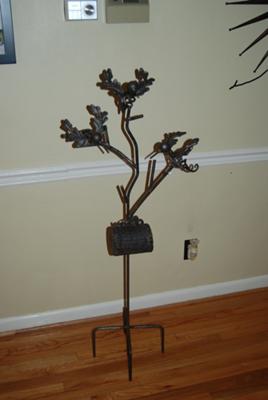
Bird Art
[From https://www.welding-advisers.com/bird-art.html]
Let us remind you that, if you are interested, we offer a no cost subscription to our Practical Welding Letter and a bonus book in pdf format to be made available for download to your computer on the subject of
PRACTICAL HARDNESS TESTING MADE SIMPLE.
Please Subscribe!.
To reach a Guide to the collection of the most important Articles from Past Issues of Practical Welding Letter, click on Welding Topics.
Back Home
PROCESSES
Site Map
Metals Knowledge
Friction Welding Processes
Friction Stir Welding
Friction Surfacing
Flash Welding Process
Stud Welding
Upset Welding
Resistance Welding Processes
Material Identification
Beam-processing Top
Can you imagine working for fun?
Watch the video...
Click on the following image to watch the SBI! TV Show!
BUILT BY:
Click on this Logo NOW!
Copyright (©) 2012, 2013, 2014, 2015, 2016, 2017
by Elia E. Levi and www.welding-advisers.com
All Rights Reserved