Friction-welding
Low cost, High yield:
SOLUTIONS with Effective, Powerful Advice
Using Friction to Weld Metals
|
Welding Problem? Solve it! with
Help from a Welding Professional Contact Us.
|
Note: To view Google Ads, Pls.
Right Click and Open in a New Window.
|
What is in here for me?
Friction-welding, a specialized process having valuable advantages and some limitations, is presented here.
Will you ever need information on Friction Welding?
Even if you may doubt it now, having a good idea of the process may help you.
Should the case present itself, you may remember it and search deeper when you need it.
In a separate page we are providing some more details on Friction Welding Equipment.
Some more details...
We are going to enter into some more detail for the class of Pressure Welding processes known and described as Friction-welding processes.
Friction-welding is a sub-class that includes variations of a process that uses the heat obtained by the transformation of mechanical energy into heat, generated through the attrition of two elements.
Under suitable conditions, that brings about a solid state joining under pressure without resorting to melting.
The Friction Welding process consists in bringing into contact two elements to be welded.
One of the two is static and the other is rotated rapidly on its axis.
As soon as the heat generated by attrition at the interface is sufficient for solid state welding without melting, the rotation is stopped.
The elements are forced together under pressure producing local forging, which concludes the intimate joining.
See Forge Welding.
The pressure also expels at the joint all surface contamination and some of the upset material, called flash.
Tip!: The interested reader wishing to study the applicability of a Friction welding solution, should be alerted that the joint (not necessarily the elements), in general, must present rotational symmetry (must look like a round button or a ring).
Friction-welding is an economical process...
Note: To view Google Ads, Please
Right Click and Open in a New Window.
|
Friction welding is economical in that it permits joining together different materials, one of which may be inexpensive.
Heat is produced cheaply, without arc or flame, without gases or fumes, without protective atmosphere,
Its quality control cost is minimal, with a guarantee of high quality welds.
Moreover the weld cycle is extremely short, so that productivity is very attractive.
Once set up the Friction-welding process is carried out by unskilled workers and could be automated.
The Friction Welding process is suitable for mass production. As such it is not an option for a general welding job shop.
However even a small shop can specialize in Friction-welding provided large orders can be secured for relatively small items to be manufactured in very large quantities.
Friction-welding has been used with success, however, for repairing expensive rejected shafts of turbine engines.
This was done by discarding the damaged end and welding in place a new section.
The result was salvaging a most expensive item with a high quality weld.
This is sufficient justification for an expensive machine and for a short run job.
Disadvantages...
The disadvantages of Friction Welding are that not every configuration is feasible.
A machine of sufficient power is needed, and for short runs the process may not be economical.
Apart from the cost of equipment, which must be suitable for the intended joints, the Friction-welding process has some costs in tooling and setup.
Those must be taken into account when calculating the cost per weld.
Tight concentricity requirements, when needed, may be difficult to meet.
Also finishing operations may be requested which sum up to the total cost.
Best quality...
The quality of the welds is very high and repeatable, as long as all the functions of the machine can be properly monitored and maintained.
It is perfectly obvious that Friction Welding can be the process of choice for certain classes of automotive parts that lend themselves to be friction welded.
The Friction-welding process is suitable for non homogeneous joints involving materials having quite different chemical, mechanical and thermal properties.
The welds produced may result of the most favorable metallurgical characteristics.
Therefore it has been used to weld a bit of expensive material (to be exploited where needed) to a stem of a simple and inexpensive one.
Exhaust valves of internal combustion engines are an example.
Other applications involve the Friction-welding of a forged part to a simple bar, a practice that has the potential of providing substantial savings.
An Article on Weld Crack Repair in a Transition Part was published (3) in Issue 50 of Practical Welding Letter for October 2007.
Click on PWL#050 to read it.
Easy preparation...
Preparation of the elements is simple and easy, provided that the design of the joint lends itself to Friction-welding.
The process is friendly to the environment.
As there is always an axial shortening of both elements, their exact length before welding must be established experimentally prior to production.
The Friction-welding process is performed with different machines.
The details of the mechanical movements may vary, but no substantial change is noted in the realization of the joint.
Some more details on this development and a few links can be found in a page on Friction Welding Equipment.
An emerging technology development, first demonstrated as a laboratory curiosity, has been recently adopted for actual production of aerospace, automotive and ship hardware.
See the dedicated page at Friction Stir Welding.
Such a weld, being in a fine grained hot worked condition, has considerable metallurgical advantages especially for aluminum alloys, like absence of porosity or oxides and very good mechanical properties.
An Article on Friction Stir Welding, one of the most important innovations of recent times, was published (2) in Issue 47 of our Practical Welding Letter for July 2007.
Click on PWL#047 to read the article.
An Article on Friction Stir Surfacing was published (2) in Issue 49 of Practical Welding Letter for September 2007. To see the article click on PWL#049.
An Article on Welding Dissimilar Metals was published (7) in Issue 97 of Practical Welding Letter for September 2011.
Click on PWL#097 to see it.
In the same Issue see also an Article on Underwater Friction Taper Plug Welding at (11).
An Article on Remotely Operated Underwater Friction Welding Technology was published (11) in Issue 134 of Practical Welding Letter for October 2014.
Click on PWL#134 to see it.
An Article on Advancements in LFW was published (7) in Issue 150 of Practical Welding Letter for February 2016.
Click on PWL#150.
An Article on Field Assisted Sintering was published (7)
in Issue 155 of Practical Welding Letter for July 2016.
Click on PWL#155.
To receive every issue of Practical Welding Letter as it is published, please subscribe.
Watch the following Video on
The Power of Friction
https://www.youtube.com/watch?v=5JbnDXw-0pM
|
* * *
Any questions or comments or feedback? Write them down and send them to us by e-mail.
Click on the Contact Us button in the NavBar at top left of every page.
Note: To view Google Ads, Please
Right Click and Open in a New Window.
|
Back Home
Site Map
PROCESSES
Friction Welding Processes
Friction Stir Welding
Friction Surfacing
Flash Welding Process
Stud Welding
Upset Welding
Resistance Welding Processes
Projection Welding
We used to remind to our readers titles and links
to our informative pages on:
- welding basics,
- welding processes,
- welding materials and
- other welding related subjects.
We are informed that publishing a long list of internal links in website pages, is judged as objectionable practice by companies that grade the relevance of the page content to users' usefulness.
Therefore, in an effort to comply with the above requirement,
we remove part of the usual list appearing in this location,
and urge our readers to use the Site Map to locate
the pages that might provide them the answers to their questions.
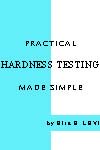
To reach a Page, listing the most important Articles from Past Issues of Practical Welding Letter, click on Topics.
For your FREE subscription to our periodic Practical Welding Letter and for downloading your FREE copy of our book right to your computer (in pdf format) PRACTICAL HARDNESS TESTING MADE SIMPLE, please Subscribe.
It is usually necessary to know the hardness of the items to weld, beforehand...
Visit the NEW Page on Welding Problems,
for looking into the causes of production hindrances.
Visit the NEW Page on Architectural Metalwork,
for reviewing a few momentuous icons of excellent fabrications.
Visit the NEW Page on Welding Overview, for a thorough
Introduction to Welding.
Visit also the NEW Page on Process-selection, for
Understanding the Selection procedure and
the NEW Page on Process-optimization
for improved productivity.
If you did not yet find what you need, why not typing your question in the following Search Box?
Friction-welding Top
Watch the following video...
POWERED BY:
Click on this Logo NOW!
Watch - The Video:
Why Don't I Work From Home?
and also
Think outside the Cube.
Copyright (c) 2003-2008, 2009, 2010, 2011, 2012, 2013, 2014, 2015, 2016, 2017
by Elia E. Levi and www.welding-advisers.com
All Rights Reserved
Friction-welding processes are highly rewarding for specialized niches of applications. See here when and why they are successfully used...