Weld-cracking:
Origins and Avoidance.
Solutions with Effective, Powerful Advice
Welding Problem? Solve it! with
Help from a Welding Professional Contact Us.
|
Note: To view Google Ads, Pls.
Right Click and Open in a New Window.
|
Weld-cracking is a most dangerous situation.
It compromises the ability of a welded structure to perform the design functions in a safe and consistent way.
Cracks are discontinuities presenting fracture.
They have two dimensions quite large relative to their opening, and a sharp tip that tends to propagate under stress.
Therefore cracks must always be avoided or eliminated.
In previous pages we briefly considered Weld Cracking as a danger and cracks as unacceptable defects (Click on Welding Defects).
We discussed some welding conditions that may promote the appearance of cracks (Click on Alloy Steels).
If you did not yet find what you need, why not typing your question in the following Search Box?
Note: To view Google Ads, Please
Right Click and Open in a New Window.
|
Here we wish to present the different types of Weld cracking discussing the conditions for their appearance and the measures that can be employed to avoid them.
Four main groups of cracking are described here, known as:
- hot cracks,
- microfissures of Heat Affected Zones,
- cold cracks and
- lamellar tearing.
1 - Hot cracks
Of the four types of cracking discussed here, hot or solidification cracks appear near the end of the solidification process in the fusion zone.
They result because of the incapacity of the molten and semisolid material to absorb without tearing the thermal shrinkage strains due to weld solidification and cooling.
Weld-cracking, formed in the weakest places like grain boundaries, relieves the associated stresses.
Some microstructures are more prone than others to the formation of solidification Weld-cracking.
The presence in the metal composition of low melting elements like sulfur, lead, bismuth etc. is deleterious.
The tendency of certain metals to exhibit hot Weld cracking is called hot shortness, caused by low-melting constituents segregated at grain boundaries.
For welding, these susceptible compositions should be avoided. (Example: free machining -steels or -stainless steels).
Welding parameters should be selected with care.
They can influence the formation of hot Weld-cracking by the rate of strain application (lower rate = lower danger).
It is higher for welding processes that cause rapid solidification and cooling.
Joint design should strive to limit the molten mass, joint gap should be contained and good fit-up should be preferred, in order to reduce shrinkage strains and Weld-cracking.
Weld speed, an important productivity factor, may have to be contained at such low levels that do not cause solidification Weld-cracking, other data being constant.
For any given alloy there may be a possible range of welding parameters that permits avoiding hot Weld-cracking.
This range is narrow for alloys with a large melting interval, that are more prone to hot shortness.
On the contrary, alloys with a narrower melt interval enjoy a larger range of possible welding parameters.
It so happens because cumulative shrinkage strains are proportional to the magnitude of that melting temperature range, that depends essentially on chemical composition.
Crater cracks are a common occurrence at the end of a weld if the welding current is interrupted abruptly.
It should instead be reduced gradually, possibly directing the arc on top of an already welded beam.
Solidification cracking susceptibility can be measured in different alloys by performing a series of tests, (Varestraint Testing) and measuring the maximum length of the induced cracks.
A short note on Varestraint Test was published (9.6) in Issue 14 of Practical Welding Letter for October 2004.
Click on PWL#014 to see it.
The results permit to rate the different compositions as to their hot Weld-cracking susceptibility.
2 - Microfissures and Heat Affected Zone Cracks
are cracks that develop in a place of partial melting occurring near the Heat Affected Zone (HAZ), bordering on the fusion line.
As partial melting occurs below the melting point of the alloy, local thermal strains can induce grain boundary separation similar to what explained above.
This occurs especially if secondary elements segregation is present along grain boundaries,
HAZ cracks, may occur with or without the presence of liquid.
Failures happen if the thermal stresses associated with the weld thermal cycle exceed the local tensile strength at the actual temperature.
The above occurs if brittle structures associated to intermetallics are present.
Some alloys undergo microstructural transformations in the Heat Affected Zone as a consequence of thermal cycles brought about by welding.
Typical is the martensitic transformation, producing a hard and brittle crack-susceptible structure, which is accompanied by a volumetric change inducing noticeable stresses.
3 - Cold cracks
Hydrogen induced delayed cold Weld-cracking occurs as a consequence of contamination with this gas being absorbed in the molten metal while welding.
Hydrogen sources should be avoided and removed: not only water and humidity must be controlled by drying and preheating.
Organic matter contamination has to be removed by cleaning and good housekeeping.
Three conditions are necessary for the formation of cold cracks:
- the presence of a certain stress,
- of a suitable microstructure and
- at least a critical level of hydrogen.
A long standing theory claimed that atomic hydrogen moving interstitially within the solid metal aggregated to molecular form with pressure increase sufficient to tear apart metallic bonds.
This has been recently challenged and replaced by a competing model involving the presence of preexisting defect sites in the metal, where, under stress, hydrogen preferentially diffuses, reducing the local cohesive strength.
Fracture occurs when the remaining strength falls below the intensified stress level.
Hydrogen would then accumulate in the newly generated voids and the process would repeat itself.
Hydrogen induced Weld-cracking is a serious cause for concern especially with high strength steels.
Preheat and postheat procedures, depending on material type but also on thickness and joint constraints, are commonly employed to reduce the danger of hydrogen Weld-cracking.
The purposes are:
- to eliminate water or moisture,
- to reduce cooling rate in order to avoid dangerous structures (untempered martensite),
- to temper and soften this hard structure if formed,
- to reduce and relieve thermal stresses, and
- to allow for hydrogen gas to escape if entrapped.
An Article on Preheating, a technique useful for reducing the risk of Weld-cracking, was published in Section 2 of Issue 37 of Practical Welding Letter for September 2006.
To read the article click on PWL#037.
4 - Lamellar Tearing
Lamellar Tearing is a kind of Weld-cracking that forms beneath a weld.
It is a dangerous condition occurring when certain plate materials presenting low ductility in the thickness (or through) direction are welded to a perpendicular element.
The reason for low ductility is generally the presence of laminations or flat type discontinuities due to flattened extraneous inclusions.
Tearing always lies within the base metal, generally outside the HAZ and parallel to the weld fusion boundary.
The problem is caused by welds that subject the base metal to high shrinkage stresses in the thickness direction.
Tearing, as well as laminations, are not visible on the outside, generally, but they can be found by ultrasonic testing.
The problem can be avoided by selecting base material having adequate ductility in the thickness direction, that has been screened by ultrasonic testing for absence of laminations or other internal defects.
It can also be managed by paying due attention to joint details and avoiding massive welds that develop significant shrinkage stresses.
Although appearing sometimes long after welding, a structure stress relieved and ultrasonically tested for lamellar tearing after welding should be considered safe.
Special design details were developed for corner joints, to put the bulk of shrinkage stresses in the direction of rolling of one of the elements, and freeing the other element from stresses in the through direction.
An Article on Lamellar Tearing was published (7) in Issue 46 of Practical Welding Letter for June 2007.
Click on PWL#046 to read it.
An Article on Stress Corrosion Cracking (SCC) was published (7) in Issue 61 of Practical Welding Letter for September 2008.
Click on PWL#061 to read it.
An Article on Cracks in Welds was published (7) in Issue 68 of Practical Welding Letter for April 2009. Click on PWL#068 to see it.
An Article on Delayed Failure was published (7) in Issue 76 of Practical Welding Letter for December 2009. Click on PWL#076 to see it.
An Article on Benefits of Low Hydrogen Filler Metal Electrodes was published (4) in Issue 141 of Practical Welding Letter for May 2015.
Click on PWL#141 to see it.
See also our new page on Hydrogen Embrittlement
To receive every issue of Practical Welding Letter as it is published, please subscribe.
Watch the following Video
Welder's Workshop Weld Cracking
https://www.youtube.com/watch?v=QfeqAMnwrOA |
* * *
Any questions or comments or feedback? Write them down and send them to us by e-mail.
Click on the Contact Us button in the NavBar at top left of every page.
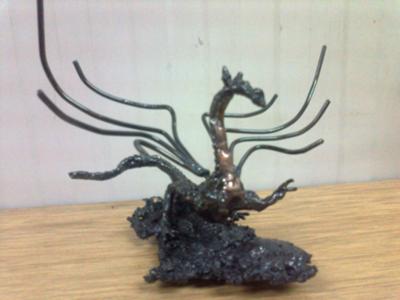
Wig Dragon
[From https://www.welding-advisers.com/my-works.html]
Let us remind you that, if you are interested, we offer a no cost subscription
to our Practical Welding Letter and a bonus book in pdf format to be sent to
your computer on PRACTICAL HARDNESS TESTING MADE SIMPLE. Click on Subscription.
Checking the hardness of an unknown material before welding may help avoid Weld-cracking.
To reach a Guide to the collection of the most important Articles from Past Issues of Practical Welding Letter, click on Welding Topics.
Note: To view Google Ads, Please
Right Click and Open in a New Window.
|
Back Home
QUALITY
Site Map
Welding Control
Welding Testing
Welding Inspection
Weld Macro
Welding Defects
Welding Liability
Welding Failures
Weldability Testing
Welding Validation
Welding Metallurgy
Residual Stress
Metallurgical Expertise
Creep Test
Hardness Test
Hardenability
Weld-cracking Top
Watch the following Video...
POWERED BY:
Click on this Logo NOW!
Watch - The Video:
Why Don't I Work From Home?
and also
Think outside the Cube.
Follow this Invitation!
Experience C2 power and flexibility in action by clicking SBI! 2.0 For You. Where SBIers share their business-building experiences first-hand. You will realize that there is nothing comparable to SBI! when you read real stories from SBIers who share how C2 has helped them expand, accelerate, build trust and monetize their sites.
|
Copyright (c) 2004-2012, 2013, 2014, 2015, 2016, 2017
by Elia E. Levi and www.welding-advisers.com
All
Rights Reserved.
Weld-cracking is a major concern for any welding job. It is important to know causes and prevention. See here...