Welding_aluminum
by different processes:
SOLUTIONS with Effective, Powerful Advice
Welding_aluminum: is it really difficult? |
Welding Problem? Solve it! with
Help from a Welding Professional Contact Us.
|
Note: To view Google Ads, Pls.
Right Click and Open in a New Window.
|
In a previous page on Welding Aluminum, a short review of Welding_aluminum was offered, including some basic properties which make aluminum alloys the natural choice for quite a large range of applications.
We presented there the main difference between aluminum alloys whose mechanical properties cannot be improved by heat treatment, and can be easily welded, and those that can be strengthened by heat treatment known as solutioning and precipitation process but cannot be readily welded.
Here we are going to enter in some more detail in the processes used for this important class of materials.
Different Processes...
Friction Welding aluminum is used for joining of aluminum alloys both to themselves and to different materials like copper alloys and stainless steels.
When applicable this process is unique in its capability to permit joining combinations which could not be performed with any other method, except possibly by Brazing with certain limiting requirements.
One recent development which has already interesting applications for space related hardware is called Friction Stir Welding.
As explained in the above page, it is designed to perform butt welding in aluminum alloys and other materials sheet and plate.
A special rotating tool is forced into the joint and moved along, between the two abutting surfaces.
Friction heats the material to a plastic state and produces a defect free weldment with finer grain size and better properties than those of the original materials.
For short reviews of this process as applied to aluminum welding, click on TWI
Different results...
RESISTANCE WELDING is used for Welding_aluminum alloys, besides other materials.
It is applicable not only for weldable alloys but also for those special alloy types (of 2xxx and 7xxx classes) hardenable by heat treatment, through solutioning and aging.
In fact resistance Welding aluminum is almost the only process recommended for this last class of materials, because its influence is local and does not degrade the material properties. Any other fusion process would impair strength, hardness and resistance to corrosion.
However some special properties affecting Welding_aluminum alloys should be considered: higher electrical and thermal conductivity (than low carbon steel): these two properties combined require higher current to perform welding in a shorter time.
When developing welding schedules for Welding aluminum, on has to consider specific aluminum alloys characteristics.
Low softening and melting temperature, lower strength, the presence of a naturally formed surface layer of aluminum oxide.
This layer produces useful corrosion resistance properties, but hinders Welding_aluminum processes if not removed.
These characteristics influence the selection of parameters for resistance Welding_aluminum. Therefore process control is much important and equipment must be capable of precisely selected settings.
Adequate surface preparation and exceptional cleanliness are essential to obtain consistent results.
Not all available aluminum alloys and conditions are resistance welded with the same ease. In particular soft alloys (in annealed condition) are prone to higher surface indentation and sheet separation which may be objectionable if not dealt with by special means.
An Article on Inserted strips in Resistance Spot Welding was published (3) in Issue 136 of Practical Welding Letter for December 2014.
Click on PWL#136 to see it.
Note: To view Google Ads, Please
Right Click and Open in a New Window.
|
Not recommended...
Gas Welding of weldable aluminum alloys in thin gauges is not outright impossible.
It requires nevertheless the use of an active flux in order to remove the oxide layer. Flux remnants must be thoroughly cleaned, removed or neutralized after welding to avoid corrosion.
Therefore oxyacetylene welding is not the preferred solution if a suitable arc welding process can be applied.
Mostly used...
Practically only GAS TUNGSTEN ARC WELDING (Tig) and GAS METAL ARC WELDING (Mig) are employed for Welding_aluminum because of their advantages where compared with other less convenient arc processes.
An Article on Feedability of Aluminum Filler Metal in GMAW was published (3) in Issue 155 of Practical Welding Letter for July 2016.
Click on PWL#155.
Again only weldable alloys should be considered, excluding 2xxx and 7xxx classes (except that special alloys were developed to allow acceptable special Welding_aluminum procedures).
They permit welding in all positions even for hard to reach spots, shielding is by inert gas, no flux is needed and quality results are achievable.
Filler metals commonly used are listed in:
- ANSI/AWS A5.3/A5.3M-99 (R2007)
- Specification for Aluminum and Aluminum Alloy Electrodes for Shielded Metal Arc Welding
- ANSI/AWS A5.10/A5.10M:2012 (ISO 18273:2004 MOD)
Specification for Bare Aluminum-Alloy Welding Electrodes and Rods
American Welding Society / 04-Oct-2012 / 46 pages
Also Castings of aluminum alloys can be repaired by Welding_aluminum, with some exceptions, preferably in fully annealed condition. Those responsive are then heat treated as required.
In summary, weldability is best for non heat treatable aluminum wrought alloys except that those which gain some hardness and strength through mechanical deformation (strain hardening like cold rolling or stretching) lose them when heated for welding.
Welding_aluminum alloys is usually performed with alternating current, except that for thin gauges also direct current reverse polarity (electrode positive) is used, with a good cleaning effect of the oxidized layer, produced on the surface by cathodic cleaning (by electrons evolving from the surface) and by bombardment of argon ions.
Alloys of series 6xxx are easily welded and can then be strengthened by heat treatment if necessary after welding.
Welding_aluminum of other heat treatable alloys is not recommended. Cast alloys fall within the same criteria depending upon their chemical composition, and their weldability varies accordingly.
Filler metal selection...
Proper filler metal selection permits Welding_aluminum of different alloys together but the choice for specific applications may be influenced by the most important feature from those following: ease of welding, strength, ductility, response to subsequent heat treatment, color match after anodizing and corrosion resistance.
An Article on the Selection of Aluminum Alloy Filler Metal was included in our Practical Welding Letter No. 04
of December 2003.
To see the article click on PWL#004.
An Article on Filler Metals for Aluminum-Lithium Alloys was published on the May 2005, Issue No. 21 of Practical Welding Letter.
To read the article click on Issue No. 21.
An Article on Weld repair of Aluminum Castings was published in Issue 42 of Practical Welding Letter for February 2007.
Click on PWL#042 to read it.
An Article on Welding Effects on Aluminum Structures was published in section (3) of Issue 44 of Practical Welding Letter for April 2007.
Click on PWL#044 to read it.
An Article on Aluminum Design Manual, 2010 Edition, was published (4) in Issue 85 of Practical Welding Letter for September 2010.
Click on PWL#085 to see it. See also hereafter.
An Article on Filler Metals for welding aluminum alloys was published (4) in Issue 163 of Practical Welding Letter for March 2017.
Click on PWL#163.
An Article on Aluminum Filler Metal Questions was published (4) in Issue 165 of Practical Welding Letter for May 2017.
Click on PWL#165.
An Article on How to Prevent Defects in arc welded Aluminum was published (7) in Issue 166 of Practical Welding Letter for June 2017.
Click on PWL#166.
An Article on Advances for Filler Metal fusing in Aluminum Robotic Welding was published (4) in Issue 169 of Practical Welding Letter for September 2017.
Click on PWL#169.
To subscribe and receive regularly by e-mail at no cost the periodic publication above, click on Subscription.
Best weld quality depends on thorough cleaning of the base metal before Welding_aluminum and should be conducted by chemical or mechanical means in order to remove not only foreign material but also the oxide layer which forms on the surface by normal exposition in air.
Other Specifications and reference documents are listed hereafter:
- AWS B2.1-22-015:2011
- Standard Welding Procedure Specification (Swps) for Gas Tungsten Arc Welding of Aluminum (M/P/S-22 to M/P/S-22), 18 through 10 Gauge, in the As-Welded Condition, with or without Backing
- ANSI/AWS C3.7-2005
- Specification for Aluminum Brazing
- ANSI/AWS D1.2/D1.2M:2008
- Structural Welding Code - Aluminum
Edition: 5th
American Welding Society / 23-Jun-2008 / 228 pages
- ANSI/AWS D3.7-2004
- Guide for Aluminum Hull Welding
- ANSI/AWS D8.14M/D8.14-2008
Specification for Automotive Weld Quality - Arc Welding of Aluminum
Edition: 2nd
American Welding Society / 23-Jun-2008 / 34 pages
- ANSI/AWS D10.7M/10.7-2008
- Guide for the Gas Shielded Arc Welding of Aluminum and Aluminum Alloy Pipe.
Edition: 4th
American Welding Society / 21-Apr-2008 / 44 pages
- ANSI/AWS PRGWA
- The Practical Reference Guide to Welding Aluminum in Commercial Applications.
American Welding Society / 2002 /
- AWS PHB-8
- Everyday Pocket Handbook for Gas Metal Arc Welding of Aluminum
- AWS PRGQA
- The Practical Reference Guide for High Quality Fusion Welding of Aluminum.
High power density processes...
Electron Beam Welding_aluminum of weldable aluminum alloys is readily performed with good results even in very deep welds.
As usual the remarkably high depth to width ratio permits to join configurations not possible with other means. The heat input being low and the heat affected zone of limited extent, there is often no remarkable damage to the mechanical properties so that further heat treatment is not required.
Also LASER Beam Welding_aluminum is performed on weldable alloys, with the usual precautions needed to insulate the weld from air.
NEW RESOURCES
Find some interesting links in a special Mid Month Bulletin Page of our PRACTICAL WELDING LETTER, designed to offer you, our interested readers, the opportunity to search the web quickly and effectively on the subject of welding Aluminum. We urge you to explore this rich source of essential knowledge. Online Resources on Aluminum and Aluminum Alloy Welding , presenting Downloads, Previews, Links and Information is now available by clicking on PWL#041B. |
Looking for more Online Reference Links?
Click on Welding Resources
A new page on Aluminum Finishing was recently added to our Website. Click on the underlined title to read it (Opens a new Window).
An alternative process for joining together overlapping sheets, even of dissimilar materials, incompatible for fusion welding, is illustrated in our new page on Clinching.
If you did not yet find what you need, why not typing your question in the following Search Box?
* * *
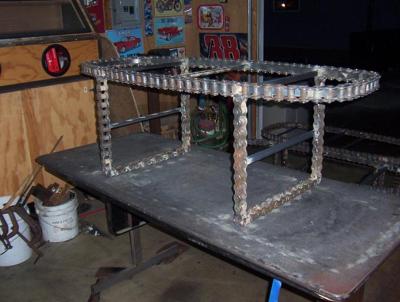
Roller Chain Table
[From https://www.welding-advisers.com/stinky.html]
Are you looking for Specifications? for Recommended Practices? For specific Information? If you need more information write us by e-mail. Click on the Contact Us button in the NavBar at top left of every page.
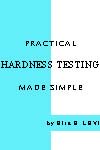
For your FREE subscription to our periodic Practical Welding Letter and for downloading your FREE copy of our booklet right to your computer (pdf format) on PRACTICAL HARDNESS TESTING MADE SIMPLE, please Subscribe!
It might help you in your job, because one must know the hardness of the work, for Welding_aluminum.
To reach a Guide to the collection of the most important Articles from Past Issues of Practical Welding Letter,
click on Welding Topics.
Note: To view Google Ads, Please
Right Click and Open in a New Window.
|
Back Home.
Browse through other website pages using the Site Map.
MATERIALS (Aluminum Welding).
Cast Iron Welding
Steel Welding
Tool Steel Welding
Alloy Steel Welding
Stainless Steel Welding
Magnesium Welding
Titanium Welding
Copper Welding
Heat Resisting Alloys Welding
Joining Lead Tin Zinc
Refractory Metals
Precious Metals
Material Identification.
Welding_aluminum Top
Watch the following Video...
POWERED BY:
Click on this Logo NOW!
Watch - The Video:
Why Don't I Work From Home?
and also
Think outside the Cube.
Follow this Invitation!
Experience C2 power and flexibility in action by clicking SBI! 2.0 For You. Where SBIers share their business-building experiences first-hand. You will realize that there is nothing comparable to SBI! when you read real stories from SBIers who share how C2 has helped them expand, accelerate, build trust and monetize their sites.
|
Copyright (©) 2003-2010, 2011, 2012, 2013, 2014, 2015, 2016, 2017
by Elia E. Levi and www.welding-advisers.com
All Rights Reserved
Which processes are used to weld aluminum alloys? Why is Resistance welding applicable to heat treatable alloys? What about alloy conditions? We should better know before trying. See here...