Welding-magnesium:
all that you need to know.
SOLUTIONS with Effective, Practical Advice
Welding Problem? Solve it! with
Help from a Welding Professional Contact Us.
|
Note: To view Google Ads, Pls.
Right Click and Open in a New Window.
|
What is in here for me?
Welding-magnesium, magnesium alloy types welding.
Weldability of magnesium, magnesium heat treatments and welding processes are some of the items developed in this Site for the benefit of interested readers.
Basic information is proposed on the materials and processes used for welding magnesium.
A special warning is included on some dangerous properties that require attention.
Welding-magnesium is currently performed either for primary manufacturing or for repair as needed, mostly by the arc processes discussed in the following.
Properties
Magnesium alloys is one of the lightest metals, with density of about 1.74 g per cubic centimeter (0.063 lb. per cu in.).
When in cast form, alloyed with Aluminum, Manganese, Rare Earths, Thorium, Zinc or Zirconium, it displays high strength to weight ratio making such alloys materials of choice whenever weight reduction is important.
Also when it is imperative to reduce inertial forces (for rapidly moving machine parts).
Magnesium is roughly 20% the weight of steel and 67% the weight of aluminum (in bodies of equal volume).
Magnesium castings exhibit remarkable damping capacity.
An Article on Magnesium Corrosion was published on the May 2005, Issue No. 21 of Practical Welding Letter.
To read the article click on PWL#021.
An Article on Filler Metals for Magnesium Alloys was published in the Issue 25 of September 2005 of Practical Welding Letter.
To read the article click on PWL#025.
An Article on Filler Metal for low temperature Magnesium Joining was published (4) in Issue 57 of Practical Welding Letter for May 2008.
To read the article click on PWL#057.
An Article on How to repair a Magnesium Saw Housing was published (11) in Issue 87 of Practical Welding Letter for November 2010.
Click on PWL#087 to see it.
An Article on Aluminum Filler Metal for High Pressure Cold Spray of Magnesium Castings was published (4) in Issue 151 of Practical Welding Letter for March 2016.
Click on PWL#151.
To receive and read all the PWL issues as they are published, please Subscribe.
Pure Magnesium melts at 650 °C (1202 °F).
Contraction from liquid to solid is 3.9 to 4.2% and from liquid at melting temperature to a solid at room temperature is 9.7%.
Magnesium is used as an alloying element in the production of certain aluminum alloys.
In cast iron foundries producing nodular cast iron, magnesium is used to make the graphite particles nodular.
It is also used for cathodic protection of other metals from corrosion.
Safety precautions must be understood and followed.
WARNING!
When Welding-magnesium or when working with magnesium one must always remember that the material is highly oxidizable and, when in form of machined turnings or powders, it will burn, if ignited, with dangerous intensity.
Machining must be performed under controlled conditions, with approved extinguishing agents ready on the spot.
Tip!: Magnesium can be easily distinguished from aluminum. It is attacked rapidly by usual inorganic acids (excluding hydrofluoric and chromic acid). It is not attacked by alkalies and caustic soda (Warning! it may be dangerous to use).
On the contrary aluminum is readily attacked by alkaline solutions and not by acids like nitric and sulfuric.
For more details click on Materials Identification.
Specifications
Cast alloys are covered by the following Specifications:
ASTM B80-09
Standard Specification for Magnesium-Alloy Sand Castings
ASTM International / 07-Dec-2009 / 11 pages
ASTM B94-07
Standard Specification for Magnesium-Alloy Die Castings
ASTM International / 01-Jun-2007 / 6 pages
ASTM B199-12
Standard Specification for Magnesium-Alloy Permanent Mold Castings
ASTM International / 01-Nov-2012 / 6 pages
Wrought alloys are covered by:
ASTM B107/B107M-12
Standard Specification for Magnesium-Alloy Extruded Bars, Rods, Profiles, Tubes, and Wire
ASTM International / 01-Nov-2012 / 19 pages
ASTM B217
Specification for Magnesium-Base Alloy Extruded Tubes
is Superseded by ASTM B107 (see above).
Filler metals for Welding-magnesium alloys are specified in:
AWS A5.19-92(R2006)
Specification for Magnesium Alloy Welding Electrodes and Rods
Two older document were cancelled:
ASTM B 448 (Document cancelled) - Specification for Magnesium-Alloy Welding Rods and Bare Electrodes
SAE AMS 4397 (Document cancelled) - Magnesium Wire, Welding.
Characteristics
Welding-magnesium alloys require lower amounts of heat for melting than most other materials because of low melting point and other favorable characteristics.
However a larger amount of distortion, relative to other metals, may arise due to high thermal conductivity and coefficient of thermal expansion.
Therefore adequate precautions must be taken.
Note: To view Google Ads, Please
Right Click and Open in a New Window.
|
Alloying Elements
As pure magnesium has too low mechanical strength to be used as is, it must be alloyed with other elements which confer improved properties.
The Mg-Al-Zn group of alloys, contains Aluminum and Zinc, which are the most common alloying elements for room temperature applications.
Alloying elements Thorium, Cerium and Zirconium (without Aluminum) are used for elevated temperature use and form the Mg-Zn-Zr group.
An increase in alloy content depresses the melting point, enlarges melting range and increases weld cracking tendency.
High alloy content need less heat for melting and also limit grain growth, showing higher Welding-magnesium efficiency.
Aluminum is the most effective ingredient in providing improved results.
In percentages of 2 to 10%, with minor additions of zinc and manganese, it increases strength and hardness.
This occurs at the expense of less ductility, without impairing weldability but making the alloy responsive to heat treatment.
Magnesium alloys containing more than 1.5% Al are susceptible to stress corrosion and must be stress relieved after welding.
Zinc combined with aluminum improves properties.
It helps to overcome harmful corrosive effects of iron and nickel impurities that may be present in magnesium alloys.
The higher the Zn content (over 1%) the higher the hot shortness, causing weld cracking.
Manganese improves yield strength (slightly) and salt-water resistance of magnesium alloys.
Higher melting point requires higher heat input to melt. Grain growth adjacent to the weld reduces strength.
Thorium or Cerium are added for improving strength at temperatures of 260 to 370 °C (500 to 700 °F). Zirconium in small amounts is a grain refiner that improves weldability.
Beryllium is sometimes added to reduce the tendency of magnesium to burn while melting.
No adverse effect on welding has been observed. It may be beneficial, in a brazing alloy, in reducing the danger of ignition during brazing in furnace.
Calcium is added in small amounts to reduce oxidation, but may increase the risk of weld cracking.
Iron, Copper and Nickel are considered objectionable impurities to be limited because they degrade the corrosion resistance of Magnesium alloys.
Processes
Welding-magnesium is generally performed by arc processes using direct current with reverse polarity (electrode positive).
Weldability varies with type from excellent to limited.
Wrought alloys are usually weldable more easily than certain cast alloys.
With Gas Metal Arc Welding-magnesium (GMAW) also known as Metal Inert Gas (Mig) three modes of metal transfer through the arc are suitable, in the following sequence arranged for increasing thicknesses, with higher currents and deposition rates:
- Short circuit mode, (with lowest current) whereby the filler touches the work many times per second and extinguishes the arc, the metal being supplied as a sequence of drops,
- Pulsed arc mode, where a special power supply provides a modulated current, the arc is not interrupted and the metal is transferred in an intermediate mode,
- Spray transfer mode (with highest current) where the metal is transferred as a spray of tiny droplets.
Of the three modes of Welding-magnesium, the second uses the most expensive (to buy and maintain) sophisticated equipment.
It should be selected only if it is demonstrated that the other modes are not suitable and that this mode provides an economic advantage.
The four most common filler metals available, are:
ER AZ61A, ER AZ101A, ER AZ92A, ER EZ33A.
Some composition similarity with the base metal is recommended, although the least costly is usually preferred where suitable.
The most used shielding gas is generally argon while mixtures with helium are acceptable.
Gas Tungsten Arc for Welding-magnesium (GTAW) also known as Tungsten Inert Gas (Tig) is more common than GMAW above.
Alternating current machines or direct current reverse polarity (electrode positive) power supplies, with high frequency current superimposed are used.
For thin sheets both are suitable, for heavier sheets alternating current is preferred as it provides deeper penetration.
Direct current straight polarity (electrode negative) is not preferred because it lacks the cathodic cleaning action.
One of the most common Welding-magnesium applications is the repair of castings either as cast or after service.
Preparation is most important and should exclude all contamination from extraneous materials.
Generous bevels should be prepared for allowing full penetration, use of backing plates is recommended.
The need for preheating when Welding-magnesium is dictated by the degree of joint restraint and by metal thickness: for thick walls and a short welding bead, it may not be required.
Preheating should be performed as needed possibly in a furnace with protective atmosphere for reducing oxidation.
One of the recommended procedures to minimize weld cracking is to weld from the center towards the sides (one half after the other). Thermal shocks should be avoided.
Stress relieving is generally performed, except that for restoring properties after substantial repair welding of castings, full heat treatment is sometimes prescribed.
Electron Beam Welding-magnesium has been used for repair of expensive casting where feasible, on alloys containing less than 1% Zinc.
The relative weldability of the different Magnesium alloys is similar to that displayed for the more common arc processes.
The conditions have to be strictly monitored because of the danger of developing voids and porosity due to the low boiling point of Magnesium and the still lower one of Zinc.
A slightly defocused beam may help in obtaining sound welds.
Laser Beam is a preferred method for Welding-magnesium because of low heat input, elevated speed and limited deformation.
However the tendency of developing porosity must be considered.
Resistance Welding-magnesium either spot or seam is performed on wrought alloys like sheets and extrusions, essentially with equipment and conditions similar to those used for aluminum.
In all cases the surface should be thoroughly degreased and, if present, the chrome-pickling protective coating should be locally removed before welding.
Although strictly speaking the feasibility of oxyacetylene Welding-magnesium cannot be ruled out, with the use of suitable fluxes, this process is not recommended because it requires complex flux neutralization procedures.
A page on Brazing Magnesium was added to this Website. Click on the link to read the page.
If you did not yet find what you need, why not typing your question in the following Search Box?
Watch the following Video on
Welding Magnesium
https://www.youtube.com/watch?v=tausy8soPzU |
* * *
Any questions or comments or feedback? Write them down and send them to us by e-mail.
Click on the Contact Us button in the NavBar at top left of every page.
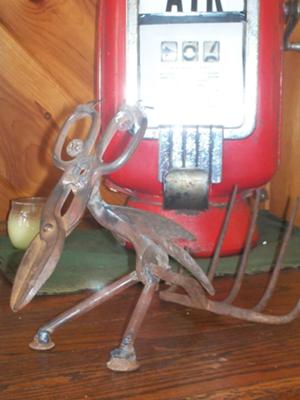
Baby Bird
[From https://www.welding-advisers.com/the-wolfwolf-studio.html]
Let us remind you that you are entitled, if you are interested, to a FREE subscription to our Practical Welding Letter, that we will send to you periodically for as long as you want, and to a FREE download, right to your computer, of our book in pdf format, designed to stress important points on PRACTICAL HARDNESS TESTING MADE SIMPLE: Please Subscribe.
Even if you know what Hardness Testing is all about, you might discover a few useful ideas, with direct application to your welding projects.
To reach a Guide to the collection of the most important Articles from Past Issues of Practical Welding Letter, click on Welding Topics.
Note: To view Google Ads, Please
Right Click and Open in a New Window.
|
Back Home
Site Map.
MATERIALS
Cast iron welding
Steel welding
Alloy Steel Welding
Tool Steel Welding
Stainless steel welding
Aluminum welding
Titanium welding
Copper welding
Heat resisting alloys welding
Joining Lead Tin Zinc
Refractory Metals
Precious Metals
Welding of Plastics
Creep Resistant Steels Welding
Joining Galvanized Steels
Material Identification.
Welding-magnesium Top
Watch the following Video...
Click on the following image to watch the SBI! TV Show!
POWERED BY:
Click on this Logo NOW!
Watch - The Video:
Why Don't I Work From Home?
and also
Think outside the Cube.
Follow this Invitation!
Experience C2 power and flexibility in action by clicking SBI! 2.0 For You. Where SBIers share their business-building experiences first-hand. You will realize that there is nothing comparable to SBI! when you read real stories from SBIers who share how C2 has helped them expand, accelerate, build trust and monetize their sites.
|
Copyright (c) 2003-2008, 2009, 2010, 2011, 2012, 2013, 2014, 2015, 2016, 2017
by Elia E. Levi and www.welding-advisers.com
All Rights Reserved
Welding-magnesium, a heavy subject for a light material.
See what it is, what it needs, what it means, how it is done.