Welding-nickel
for special benefits.
SOLUTIONS with Effective, Practical Advice
Welding Nickel Alloys Expertise
|
Welding Problem? Solve it! with
Help from a Welding Professional Contact Us.
|
Note: To view Google Ads, Pls.
Right Click and Open in a New Window.
|
Welding-nickel is an important subject.
Welding is required for fabrication of specific applications of Nickel and nickel alloys.
These materials were developed in a large number of alloys for their exceptional properties.
Among other advantages they have remarkable resistance to Heat and/or Corrosion.
A previous page dedicated to heat resisting alloys includes also a discussion of some Cobalt alloys.
Collectively, they display suitable properties for demanding applications.
See Heat Resisting Alloys Welding.
Nickel and nickel alloys in wrought form are quite ductile.
Certain alloys, developed primarily for high temperature service, resist deformation even when hot (they were designed that way).
Welding-nickel cast alloys may be difficult, especially those with high silicon.
Precipitation Hardening Cast nickel alloy blades for gas turbine engines, are a special case.
Special casting techniques provide them with directionally solidified or single crystals, essential for their unique performance.
They are built with integral air cooling channels.
Those cast blades are further protected from oxidation and erosion by proprietary coatings.
Welding them with traditional means would destroy their special properties.
Therefore they cannot be repaired except by very special welding techniques developed for this purpose.
In fact local weld deposition for repair buildup has been attempted with some success both by Electron Beam and by Laser Beam Welding.
Note: To view Google Ads, Please
Right Click and Open in a New Window.
|
This remains a very special application as detailed hereafter.
Surface restoration of damaged expensive parts has been performed with Welding-nickel by high energy beams.
See the Laser fused metal powders article, published (2) in issue 43 of Practical Welding Letter for March 2007.
Click on PWL#043 to read it.
An Article on Weldability of Cast Nickel Superalloys was published (11) in Issue 98 of Practical Welding Letter for October 2011.
Click on PWL#098 to see it.
Welding-nickel is done mostly with arc welding and with high energy processes. Oxyacetylene welding should not be employed.
Two general classes of nickel alloys are available.
Those that derive their strength properties from their composition are known as Solid Solution alloys.
These are generally weldable by Welding-nickel, and serviceable in as welded condition.
The Precipitation Hardening alloys develop their remarkable mechanical properties because of two combined factors.
- A finely tuned alloy composition, and
- a delicately balanced heat treatment.
These result in developing suitable micro-structures capable of exceptional strength even at high heat.
Using Welding-nickel to join these alloys (that usually contain small amounts of aluminum and titanium), would require the complete heat treatment cycle, including solutioning and precipitation, to be performed.
Only in this case they would exhibit the special properties they are capable of.
Cleaning is most important in Welding-nickel.
At molten metal temperature many contaminants like sulfur, lead and others, as well as oil, paint and dirt if present on the surface, might find their way into the weld.
Such contamination would have harmful consequences. Oxides should also be removed.
Preheating is usually not needed except for avoiding water condensation in cold weather.
Postweld treatment is normally not required to restore corrosion resistance, however full solution treatment is sometimes recommended.
Joint design is quite normal for Welding-nickel except that special attention should be paid to accessibility.
The opening must be sufficient for electrode or torch to reach the bottom of the joint.
As penetration tends to be lower, when Welding-nickel alloys are compared to steels, thinner lands should be designed in the joint root.
Beveling is needed only for material thicker than about 2.4 mm except if Welding-nickel with high energy processes (Electron- and Laser-Beam), or with Plasma arc over a certain thickness.
Fixtures and clamping tools should be used to keep aligned components in place, minimize buckling and reduce distortion.
Backing bars should be made of copper, and include a contoured groove to permit penetration and avoid gas entrapment.
If Welding-nickel alloy thin sheet metal parts, fixtured with firm hold-down force, the thermal expansion may set in the weld favorable compressive stresses.
For Shielded Metal Arc Welding-nickel, (SMAW), weaving of the electrode is recommended, to melt and wet the sides of the groove.
This is because molten nickel metal is not free-flowing as iron base alloys, and therefore it must be deposited where needed.
All beads should show slightly convex profile.
Gas Tungsten Arc Welding-nickel alloys (GTAW), both manual and mechanized, is performed with Direct Current with Electrode Negative (DCEN - Straight Polarity).
Argon is the shielding gas usually selected, while helium or mixtures of the two may be used in special cases.
Filler metal are normally similar in composition to the base metals to join.
2% Thoriated tungsten electrodes are preferably selected. They should not contact the base metal.
High frequency circuits permit arc starting without touching and contaminating the electrode.
Arc length should be kept as short as practicable.
The hot end of filler metal should be kept always in the shielding gas.
The underside of groove welds has to be protected from oxidation by having shielding gas flowing from the backing bar.
Gas Metal Arc Welding-nickel alloys is used when greater deposition rates are needed than available with GTAW.
That occurs practically for thicker items and longer joints.
The metal transfer mode should be selected as suitable for the application.
Direct Current with Electrode Positive (DCEP - Reverse Polarity) should be used.
Filler metal should be selected as required by application, and dependent on the type of base metal.
Flux-Cored Arc Welding uses special filler metal wires that contain a flux inside, at their core.
They may provide better oxidation protection and increased productivity.
For Welding-nickel, shielding gas is generally used as an additional precaution against air contamination, besides the flux.
Plasma Arc Welding (PAW) is used when special benefits can be obtained from using the keyhole technique, without adding filler metal up to about 9 mm (0.3 in).
Overlaying is the process of Welding-nickel alloys on the surface of less expensive material like steel.
Iron dilution should be kept to a minimum, by using buffer layers of acceptable Transitional materials.
High deposition rate processes are used, like GMAW and Submerged Arc Welding (SAW).
This last process must be performed by keeping the weld flat, so that rotating positioners must be employed for the internal overlaying of large cylinders.
If iron dilution is not kept under control, cracking may occur in the weld.
If this happens, all precautions must implemented to reduce it or to better insulate the last layers from the firsts.
The following American Welding Society documents classify the nickel base welding filler metals:
ANSI/AWS A5.11/A5.11M:2010
Specification for Nickel and Nickel Alloy Welding Electrodes for Shielded Metal Arc Welding
Edition: 10th
American Welding Society / 15-Dec-2009 / 52 pages
ANSI/AWS A5.14/A5.14M:2011
Specification for Nickel and Nickel-Alloy Bare Welding Electrodes and Rods
American Welding Society / 01-Nov-2011 / 42 pages
ANSI/AWS A5.34/A5.34M-2007
Specification for Nickel-Alloy Electrodes for Flux Cored ArcWelding
American Welding Society, 12-Jul-2007, 42 pages
Tables reporting selected designations and compositions are published in a separate page at
Welding Nickel Tables.
An Article on Filler Metals for Welding Nickel was published (4) in Issue 62 of Practical Welding Letter for October 2008.
Click on PWL#062 to read it.
An Article on Welding Nitinol was published (8) in Issue 66 of Practical Welding Letter for February 2009. Click on PWL#066 to see it.
A new page on Welding Nitinol was recently added to this Website.
Click on the link to read it.
An Article on welding Stainless to Nickel alloy 600 was published (3) on Issue 81 of Practical Welding Letter for May 2010.
Click on PWL#081 to see it.
An Article on Problems with Alloy 20 Overlays was published (11) in Issue 93 of Practical Welding Letter for May 2011.
Click on PWL#093 to see it.
An Article on Large Power Generation Components was published (11) in Issue 102 of Practical Welding Letter for February 2012.
Click on PWL#102 to see it.
An Article on Advanced Turbine Airfoil Development was published (2) in Issue 142 of Practical Welding Letter for June 2015.
Click on PWL#142 to see it.
An Article on The welding of Nickel and Cobalt alloys was published (7) in Issue 145 of Practical Welding Letter for September 2015.
Click on PWL#145.
A new Mid Month Bulletin with Resources on Nickel, published as Part 7 of the collection of the Project
Build your own Online Materials Encyclopedia, was
recently released as Bulletin 123.
Click on Bulletin 123.
For the Metals Knowledge page, click on Metals Knowledge.
To receive at no cost every month the above publication in your email Inbox, please subscribe.
RESOURCES
Find some interesting links in a special Mid Month Bulletin Page of our PRACTICAL WELDING LETTER, designed to offer you, our interested readers, the opportunity to search the web quickly and effectively on the subject of Welding Stainless Steels and Nickel Alloys.
We urge you to explore this rich source of essential knowledge.
Online Resources on
Welding Stainless Steels and Nickel Alloys, presenting Articles, Downloads, Links, Previews and Information are now available by clicking on PWL#033B. |
Do you need more Online References on additional welding subjects?
Click on Welding Resources.
Watch the following Video on
Imagine the World of Nickel
https://www.youtube.com/watch?v=d7Ji7KgbEbc&list=UUiHPdnqPHaWFaI6tVCrEkhA&index=1 |
* * *
Any questions or comments or feedback? Write them down and send them to us by e-mail.
Click on the Contact Us button in the NavBar at top left of every page or on Contact Us.
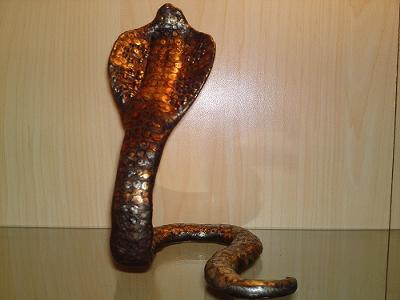
Untitled
[From https://www.welding-advisers.com/100-stainless-steel.html]
Let us remind you that, if you are interested, we offer a no cost subscription to our Practical Welding Letter and a bonus book in pdf format to be made available for download to your computer on the subject of
PRACTICAL HARDNESS TESTING MADE SIMPLE. Please Subscribe.
To reach a Guide to the Title collection of the most important Articles from Past Issues of Practical Welding Letter,
click on Welding Topics.
Note: To view Google Ads, Please
Right Click and Open in a New Window.
|
Back Home
Processes
Site Map
Cast Iron Welding
Steel Welding
Alloy Steel Welding
Welding High Yield Steels
Tool Steel Welding
Stainless Steel Welding
Welding Duplex Stainless Steel
Welding Nitinol
Heat Resisting Alloys Welding
Refractory Metals Welding
Creep Resistant Steels Welding
Welding Molybdenum
Welding Cobalt
Welding Ductile Iron
Brazing Aluminum
Brazing Copper
If you did not yet find what you need, why not typing your question in the following Search Box?
Welding-nickel Top
Watch the following Video...
Click on the following image to watch the SBI! TV Show!
POWERED BY:
Click on this Logo NOW!
Watch - The Video:
Why Don't I Work From Home?
and also
Think outside the Cube.
Follow this Invitation!
Experience C2 power and flexibility in action by clicking SBI! 2.0 For You. Where SBIers share their business-building experiences first-hand. You will realize that there is nothing comparable to SBI! when you read real stories from SBIers who share how C2 has helped them expand, accelerate, build trust and monetize their sites.
|
Copyright (©) 2008, 2009, 2010, 2011, 2012, 2013, 2014, 2015, 2016, 2017
by Elia E. Levi and www.welding-advisers.com
All Rights Reserved.