Abrasive-waterjet-cutting
can benefit you too!
SOLUTIONS with Effective, Practical Advice
Cold Cutting for Explosives and Other Cases |
Abrasive-waterjet-cutting is, besides sawing, a continuous cold cutting process.
[Note: - Punching, piercing and blanking could also be called cold cutting processes.
For completeness one should add that, in case of necessity, drilling a sequence of overlapping holes could qualify as a cold process for cutting metal.]
As such it must be used whenever cutting produced by using heat would cause explosions.
Examples are disposal of obsolete ammunition or breaking up of containers with traces of flammable liquids or gases.
Furthermore in the cold process there is no heat damage to the material and the work hardening of the cut edges is minimal.
However, if the original material was under the influence of internal residual stresses, the cutting process would most probably disturb their equilibrium, so that the cut part would react by deforming.
Warping is not due to the Abrasive-waterjet-cutting but to unpredictable relief of residual internal stresses.
A short introduction to this process was presented in section 7 of issue 47 of Practical Welding Letter for July 2007. See PWL#047.
Here we would like to add more details and technical data.
Abrasive-waterjet-cutting Types
Two main versions of the process are in use for quite different applications.
In the first, called Water jet cutting, only water is used. Water jet cutting is used to process soft materials like paper and foodstuff.
In the second, called Abrasive-waterjet-cutting, abrasive particles are dragged into the water stream and impelled at high speed against the target. Abrasive-waterjet-cutting cuts hard materials.
Both the simple waterjet and the abrasive waterjet have their different typical applications. While the pure waterjet cuts soft materials, the abrasive waterjet cuts hard materials, such as metals, stone, concrete, composites and ceramics.
Water jet
The Water-jet-cutting action consists essentially in localized erosion caused by water under high pressure and supersonic velocity that precisely cuts through and grinds away small amounts of material.
The largest uses for pure waterjet cutting are disposable diapers, tissue paper, automotive interiors and soft, light materials like fiberglass insulation up to 61 cm (24”) thick. It is a very quick and economic operation, typically running non-stop day and night.
Abrasive jet
The addition of an abrasive substance powder of a specific mesh, changes the process into Abrasive-waterjet-cutting, also called hydroabrasive or abrasive jet machining, permitting severing of hard materials or metal pieces of substantial thickness.
The abrasive garnet, which is essentially the abrasive material used on sand paper, is very important for the cutting speed and edge quality. The following sizes are commonly used:
- 120 Mesh (about 125 micrometer) – produces smooth surface,
- 80 Mesh (about 180 micrometer) – most common, for general purpose,
- 50 Mesh (about 300 micrometer) – used for rough cuts.
Finer abrasives (larger mesh number) produce slower cuts and smoother surfaces. In general speed of cut is inversely proportional to quality of finishing and to accuracy of cutting.
It should be understood that the garnet in any given Mesh number, includes different proportions of various powder grain sizes, the majority of which (about 40 to 60%), but never the total quantity, has the specified mesh size.
Although inexpensive, garnet represents the largest part of consumable costs of any Abrasive-waterjet-cutting operation and cannot be recovered. Garnet consumption can be assumed to be between 0.25 to 0.70 kg/min (0.5 to 1.5 lbs/minute).
Depending on the material to cut, the actual parameters and the speed of cutting, the kerf or gap produced by cutting can be between 0.8 - 2.5 mm (0.030 - 0.100 inch). Different materials can be stacked for cutting.
Design Tips
Designing tabs is one of the techniques used to retain small parts in place until the end of the cutting session. In general much thought should be invested in the design stage, not only to develop an economic cutting process but also to save on later operations like assembling and welding.
Corners should be designed with special attention. Changing an internal corner to an arc instead of an angle, will permit much higher cutting speeds.
External corners, wherever possible, are now approached at full speed by exiting into the scrap until the bottom portion of the jet, which lags behind, has passed the corner. Then the jet is addressed to come back quickly for the next leg. Modern software can address automatically this technique called corner passing.
Cutting time may be reduced if it is possible to connect each new hole to the perimeter of the part instead of piercing through them one by one.
Machine details
All water pumps above 69 MPa (10 ksi) are plunger pumps.
Generally Abrasive-waterjet-cutting machines include inlet water filters, a 1 micron and a 0.45 micron cartridge filter, a booster pump that brings water to about 1.3 MPa (190 psi), an intensifier which is a reciprocating double action hydraulic plunger pump, and a shock attenuator.
In practice however there are quite few Abrasive-waterjet-cutting systems operating above 379 MPa (55 ksi), because of the very high maintenance costs caused by early failures at higher pressures.
The pressure ranges usually between 207 - 414 MPa (30 - 60 ksi), the jet speed between 520 - 914 m/s (1700 - 3000 feet/second). In other words at about 276 MPa (40 ksi) the stream leaves the orifice at Mach 2, and at 414 MPa (60 ksi) the speed is over Mach 3. The flow rate can be anywhere between 0.4 - 19 liter/min (0.1 - 5 gal/minute).
In waterjet cutting equipment the orifice through which pressurized water is passing, is generally made of synthetic sapphire, with a diameter of 0.1 - 0.25 mm (0.004 - 0.010").
For abrasive cutting the mixing tube, where the abrasive particles are added to the water stream to be accelerated, is an expendable item of relatively short life because it is quickly eroded.
Mixing tubes are approximately 75 mm (3 inches) long, 6 mm (1/4 inch) in diameter, and have orifices ranging from 0.5 to 1.5 mm (0.020 to 0.060 inch), the most common being probably 1 mm (0.040 inch). The stream jet diameter is between 0.5 and 2.3 mm (0.020 - 0.090 inch).
The standoff distance between the mixing tube and the target material is typically 0.5 - 5 mm (0.010 to 0.200 inch).
New Equipment - Economic considerations
When looking for new Abrasive-waterjet-cutting equipment one should match it as much as possible with the work it is intended to perform. A thorough economic study should be conducted to guarantee the Return on Investment.
A production program involving high volumes of a limited selection of different parts permits to match quite precisely the preferred machine features to performance requirements and to foresee quite accurately the actual costs.
A universal machine capable of cutting any material and shape at short notice for a range of customers, each one with special requirements, is much more difficult to specify for economic exploitation.
While the average speed of cutting for given materials and equipment can be found in different tables, it is doubtful if it is meaningful in general. In fact, by examining the trace drawn by software on specific parts (with different colors representing different speeds) one can see that speed is constantly changing depending on geometric features. The purpose is to minimize the total cutting time while meeting accuracy and surface finish requirements.
When exploring the performance of new machines one should remember that position accuracy is important, as well as straightness, flatness, and parallelism of the linear rails.
Software
Special techniques are embedded in software for quick piercing of even thick material by imparting to and fro movements of about 2.5 mm (0.10 in), called wiggle piercing, that permit rapid material removal.
Another software based method called dynamic piercing permits to adjust automatically the length of pierce and the speed to minimize the time.
Eliminating unwanted taper cut is one of the important problems of Abrasive-waterjet-cutting, noticeable at any given thickness for certain cutting speeds. It is solved mainly by using modern software to control the machine and tilting the head.
Fixturing
Although Abrasive-waterjet-cutting does not exert noticeable force on the material, it is imperative to fixture it adequately to avoid lateral movements of the workpiece that will compromise accuracy of cut.
Abrasive-waterjet-cutting can be performed underwater by specialized operators without danger to plants or animals and to marine life and environment.
An Article on Coating Removal by Abrasive Water Jet was published (11) in Issue 64 of Practical Welding Letter for December 2008. Click on PWL#064 for reading it.
An Article on Traceability in Automated Cutting was published (2) in Issue 146 of Practical Welding Letter for October 2015.
Click on PWL#146.
Resources
A collection of Abrasive-waterjet-cutting resources appears in our
Mid Month Bulletin for June 2008. Click on PWL#058B to see it.
* * *
Click on the link.
Any questions or comments or feedback? Write them down and send them to us by e-mail.
Click on the Contact Us button in the NavBar at top left of every page.
* * *
Watch the following Video on
High Pressure Abrasive Waterjet Cutting Demonstration
https://www.youtube.com/watch?v=GCH2BSfLJ70
|
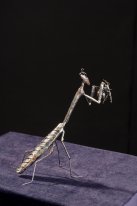
Insect
[From https://www.welding-advisers.com/nature.html]
Let us remind you that, if you are interested, we offer a no cost subscription to our Practical Welding Letter and a bonus book in pdf format to be made available for download to your computer on the subject of
PRACTICAL HARDNESS TESTING MADE SIMPLE. Click on Subscription.
To reach a Guide to the collection of the most important Articles from Past Issues of Practical Welding Letter, click on Welding Topics.
Back Home
Processes
Site Map
Welding Overview
Process-selection
Cutting
Electrical Discharge Cutting
Micro Welding Processes
Additional Processes
Cold welding
Ultrasonic Welding
Explosion Welding
Magnetic Pulse Welding
If you did not yet find what you need, why not typing your question in the following Search Box?
Abrasive-waterjet-cutting Top
Can you think of Business without Boundaries?
Watch at it in the following Video...
Click on the following image to watch the SBI! TV Show!
POWERED BY:
Click on this Logo NOW!
Copyright (©) 2008, 2009, 2010, 2011, 2012, 2013, 2014, 2015, 2016, 2017 by
Elia E. Levi and
www.welding-advisers.com
All Rights Reserved