Brazing-ceramic
Heat and Environment Compatible.
SOLUTIONS with Effective, Practical Advice
Brazing-ceramic is a special case of joining materials.
The technologies developed to perform joining of ceramics to themselves or to other materials are different from most other brazing processes.
Maybe you don't need them just now, OK. What about browsing rapidly hereafter to see if something catches your attention? One never knows when such a knowledge might become handy...
Ceramics, as everybody knows, are hard and brittle with nil ductility, and limited tolerance for tensile stresses.
Therefore if possible, ceramics are designed to be stressed in compression.
Although used as thermal insulators, they are sensitive to thermal shocks.
However, within limits, their properties can now be adapted to intended uses, especially by including in the mass strengthening (reinforcing) particles, fibers or whiskers.
And also by causing process induced structural transformations to enhance their suitability to various applications.
Brazing-ceramic Secrets
The main differences in Brazing-ceramic as opposed to metals, stem from the fact that most regular brazing materials do not wet ceramics.
This is due to basic physical properties of these materials, like their strong ionic and covalent bonding.
Furthermore, as ceramics have greater thermodynamic stability than metals, strong chemical bonds to enhance adhesion are not easy to form.
In the present increasing use of ceramics, due to the economic importance of joining them, of the many different methods applicable to perform acceptable joints, the most important and adaptable is probably still Brazing-ceramic.
Earlier ceramics were intended to withstand service at room temperature, essentially displaying insulating properties and wear resistance (in absence of shocks).
The development of more advanced types was promoted by the challenge to confront service conditions at elevated temperatures, in oxidizing or corrosive environments with substantial mechanical properties.
In particular there is a major drive to find uses for ceramic in thermal engines and in energy producing facilities for recovering waste heat. All these may need Brazing-ceramic.
The new developments are now called structural ceramics to signify their ability to meet exacting requirements in demanding service conditions.
It should be noted that ceramics can be monolithic or ceramic matrix composites.
Within each type designation or family, say Alumina, various classes are included that, depending on processing parameters, may exhibit quite different structural and mechanical properties.
Another consideration to keep in mind is that it may be quite difficult if not impossible to get tabulated design properties from handbooks or manuals.
That is because test results depend heavily upon specimen preparation and size, and on the type of test.
Also joint design can have much influence on the success of the Brazing-ceramic joining process.
The reason is the substantial difference in Coefficient of Thermal Expansion (CTE) between ceramics and metals, a fact that may introduce high stresses and possibly cracks conducive to failures.
Only exceptionally one can find a ceramic having CTE in the range of some low-expansion metals, a quite rare and welcome occurrence for performing Brazing-ceramic successfully.
One strategy often employed for bridging the gap in CTE values consists in designing joints to be stressed in compression.
Or, for widely different values of CTE, to interpose intermediate materials to provide a gradual passage from the minimum to the maximum of that property.
To promote wetting of ceramics by filler metal and its adhesion to the surface, the following techniques are used:
1) - Indirect Brazing-ceramic by first coating the ceramic surface in the joint by a material, usually a metal, suitable to be wetted by a regular filler metal that would not wet untreated ceramic surfaces.
The metallic coating acts as a transition material between metal and ceramic. Care must be taken to avoid that the coating sintering heat cycle crack the ceramic.
Typical in this class is the well known Molybdenum-Manganese coating. A slurry of specially prepared powders is applied to the ceramic as a paint.
It is then fired in a hydrogen atmosphere furnace at about 1500 °C (2730 °F) that causes glassy materials from the ceramic to migrate to the metal powder bonding it to the surface.
Other applied coating techniques resort to physical vapor deposition (PVD) for sputtering metals. Brazing-ceramic is then performed with regular brazing filler metals suitable to the metal to be joined.
2) - Direct Brazing-ceramic by using Active Filler Metals containing special alloying elements. The addition to regular silver base brazing alloys, of metals having strong affinity for the elements constituting the ceramic promotes wetting and adhesion.
Thus, metals having strong affinity for oxygen, like titanium, aluminum, zirconium, hafnium, lithium, silicon or manganese help conventional brazing alloys in wetting oxide ceramics without special preparation.
Metals that react with silicon, carbon or nitrogen help wetting of silicon carbide or silicon nitride. Quite a few Active Filler Metals were developed over the years for scientific investigations and some of these are available commercially from known manufacturers (GTE Wesgo, Degussa AG, Lucas-Milhaupt, Handy & Harman).
It seems improbable though, that off the shelf materials can be procured and used in new applications of standard Brazing-ceramic processes without thorough study and preparation.
Two other cases should be presented in this context due to their large diffusion. One is the brazing of carbide tips to steel shanks. Carbide tools are usually manufactured by sintering titanium-, tantalum- or niobium-carbide with cobalt binder. Other carbides and other metal binders are also used.
Silver base brazing filler metals containing nickel, like BAg-3, BAg-4 and BAg-22 (see Table in Brazing Stainless Steel) have been successfully used. Tungsten carbide tools need a special sandwich filler metal including a copper shim to reduce residual stresses.
The other case refers to Silicon carbide tools, brazed using a Titanium base filler metal, or a titanium containing silver-copper or nickel titanium brazing alloys.
In conclusion Brazing-ceramic although not simple to perform is a necessity if the special properties of ceramic materials of the most diverse types have to be exploited in actual implements. A thorough study and experimental development must be devoted as needed to obtain successful results.
The Special Mid August Bulletin 64, attached to our Practical Welding Letter issue 96 for August 2011, includes a rich Resources List of Online Links to readily available Information on Ceramic Brazing.
To find it Click on PWL#096 and search towards the bottom of the Publication, past the end of the regular Letter.
An Article on Selecting Active Brazing Filler Metal was published (4) in Issue 97 of Practical Welding Letter for September 2011.
Click on PWL#097 to see it.
An Article on Joining SiC: Multiphase Braze Alloy Interlayer was published (4) in Issue 102 of Practical Welding Letter for February 2012.
Click on PWL#102 to see it.
An Article on Amorphous Filler Metal for Vacuum Brazing Ceramics to Titanium was published (4) in Issue 136 of Practical Welding Letter for December 2014.
Click on PWL#136 to see it.
An Article on Advanced Microwave Brazing was published (2) in Issue 161 of Practical Welding Letter for January 2017.
Click on PWL#161.
An Article on Nanoparticles Doping of a MoNi Brazing Filler was published (4) in Issue 162 of Practical Welding Letter for February 2017.
Click on PWL#162.
An Article on Sinter Brazing was published (3) in Issue 166 of Practical Welding Letter for June 2017.
Click on PWL#166.
To get at no cost all new issues of Practical Welding Letter as they are published, please Subscribe!
For further study see:
AWS BRH
Brazing Handbook,
Fifth Edition
American Welding Society, 01-Jan-2006, 700 pages
An excellent monograph on the subject is available from page 948 to 960 in Volume 6 of ASM Handbook.
ASM Handbook:
Welding, Brazing & Soldering
Olson, David L.
9th Ed. Vol. 6
ASM International, 01-Jan-1993, 1299 pages
Note: - Although the above link shows a page declaring that the Volume 6 is now replaced by Volume 6A, this is not exact. The new Volume 6A is dedicated to Fundamentals of Welding and contains some revised articles from the previous volume besides many new articles. However many subjects treated in Volume 6 are missing from the new.
Interested Readers should explore both volumes (in a library) if they want to avoid surprises when purchasing.
* * *
Any questions or comments or feedback? Write them down and send them to us by e-mail.
Scores of readers got the answers and even thanked us for that...
See also Welding and related FAQ.
Click on the Contact Us button in the NavBar at top left of every page.
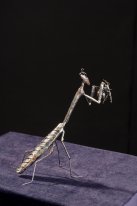
Insect
[From https://www.welding-advisers.com/nature.html]
Let us remind you that, if you are interested, we offer a
no cost subscription to our Practical Welding Letter and a bonus book in pdf format to be made available for download to your computer on the subject of
PRACTICAL HARDNESS TESTING MADE SIMPLE.
Please Subscribe!
To reach a Guide to the collection of the most important Articles from Past Issues of Practical Welding Letter, click on Welding Topics.
Back Home
Processes
Site Map
Brazing
Brazing Joint Design
Brazing Heating
Brazing Aluminum
Brazing Copper
Brazing Stainless Steel
Brazing Cast Iron
Brazing Titanium
Brazing Steel
Brazing Nickel
Brazing Magnesium
Brazing Beryllium
Brazing Graphite
Brazing Inspection
If you did not yet find what you need, why not typing your question in the following Search Box?
Brazing-ceramic Top
Would you mind to check Social Media?
Watch the video...
Click on the following image to watch the SBI! TV Show!
POWERED BY:
Click on this Logo NOW!
Copyright (©) 2008, 2009, 2010, 2011, 2012, 2013, 2014, 2015, 2016, 2017
by Elia E. Levi and www.welding-advisers.com
All Rights Reserved