Brazing-heating:
Which is the Best Method?
SOLUTIONS with Effective, Practical Advice
Brazing Problem? Solve it! with
Help from a Welding Professional Contact Us.
|
This Brazing-heating page describes various methods used as the source of heat.
Heat is needed for melting the brazing filler metal in order to perform brazed joints.
In previous pages we introduced Brazing in general and we described the principles of suitable Brazing Joint Design.
Brazing-heating Methods
Here we describe the main processes according to the source or method of Brazing-heating:
- Torch Brazing
- Furnace Brazing
- Dip Brazing
- Induction Brazing
- Resistance Brazing
- Diffusion Brazing
- Infrared Brazing
Torch Brazing
Several types of gas mixtures can be used for applying Brazing-heating by suitable hand torches.
How should the applicable mixtures be selected? Of course for the minimum cost, once they are suitable for providing heat and temperature required for the specific brazing.
This depends on the mass to heat and on the melting temperature of the brazing filler metal selected.
Fuels like acetylene, natural gas, MAPP, butane, propane and air, possibly compressed, or oxygen are among the most popular gases.
And what is a torch? A brazing torch is indistinguishable from a welding torch. This means that one torch can do both jobs. That is part of the economy of these processes.
You have essentially a handle, a mixer, that is the part where the gases mix, and one of a set of tips of different sizes, for various jobs. And valves to control the flow of each gas.
Gas cylinders, regulators, hoses and flame lighter complete the equipment, besides the personal protection gear not to be forgotten.
The simplest Brazing-heating operation is that performed by manually holding the torch in one hand, while in the other the brazing filler rod or wire is held, to be dipped in the flux as needed.
The progress is visually controlled by coordinating Brazing heating up, filler addition, molten metal distribution and cooling down, by personnel with adequate skill obtained during a short training and practicing.
Although labor intensive, this process can be economic for low production quantities as the equipment is inexpensive and readily available.
Set up is easy because elements must assemble snugly to fit with capillary gap [usually between 0.05 and 0.13 mm (.002" and .005") for most materials], does not need fixturing for usual configurations and provides excellent results.
Tip!: when fixing a fitting onto a tube, it may be necessary to improve wetting (and results) by introducing a mechanical movement. An accepted procedure is to provide a quarter of a circle motion and back to one of the elements, while the brazing alloy is in the molten state, as the movement helps the filler wet all the joint surface and displace any excess flux.
The surfaces must be clean from all contaminant, like paint, oil, grease, but a flux has to be provided for reducing the oxides forming on heating.
Filler material is preferably fed from one end of the joint, so that its appearance at the other end after joining is an indication of correct filling.
The Brazing-heating flame should be neutral or slightly reducing. The base metal should be heated only with the external envelope of the flame, avoiding contact with its inner bright cone, where temperature is much higher.
If the assembly elements to be brazed have different thicknesses, the thicker material should be heated first, so that both elements reach together the processing temperature. Direct applying the flame on the filler metal should be avoided.
For a selection of modern OXY-Gas Welding and Brazing Equipment, Torches and Kits, you may wish to have a look at My Store. |
Special torches with multiple tips may be used for supplying extensive Brazing-heating, and brazing machines that provide relative movement of parts and torches can be employed for brazing economically large quantities of similar objects.
ANSI/AWS C3.4M/C3.4:2007
Specification for Torch Brazing
American Welding Society, 24-Aug-2007, 26 pages
An Article on Manual Torch Brazing was published (3) in Issue 113 of Practical Welding Letter for January 2013.
Click on PWL#113 to see it.
To get at no cost each issue of PWL as it is published, please subscribe.
Furnace Brazing
Brazing-heating application in a furnace can be economic for processing many parts at a time or for performing many joints at once in a large and complex part.
While many furnaces are heated by electric elements, gas or flame may be used for Brazing-heating provided the flame do not impinge directly on the work load.
Using protective atmosphere in the furnace permits brazing without using a flux, as oxygen is excluded from contact with hot parts.
Some materials like titanium alloys can be successfully brazed only in high vacuum furnaces, a very effective type of protective environment.
The components to be brazed must be cleaned, then assembled, possibly held in place by self jigging, and the right amount of filler metal must be put in or near the joint (preplaced). Since Brazing-heating must be applied gradually and homogeneously, distortion is avoided.
Batch furnaces operate by cycles: the charge or work load is introduced at room temperature, and it is removed from the furnace when cold once again after a full brazing cycle is completed.
Air tight furnaces can be filled with protective atmospheres consisting of combustible gases, if suitable precautions are taken. Inert gas must be used to dispel the air at start up and shut down, and in cases of accidental power failure.
Failing to do so may permit the formation of explosive mixtures of air with combustible fuel gases. Those mixtures will explode when in contact with hot parts.
Furnaces which are not air tight can be used for heating if Brazing-heating is performed in a sealed retort, an air tight box filled with inert gas or other protective atmosphere. The retort, once charged and purged, is introduced in the hot furnace for performing brazing of the assemblies inside it.
In principle any inert gas should be adequate but even tiny proportions of humidity in the gas would oxidize the parts and hinder brazing. As it is quite difficult to provide absolutely dried gas, active gases capable of reducing oxides are preferred.
Combustible gases or mixtures are provided continuously to the furnace (or the retort) at slightly higher a pressure than that of the environment, just to assure that air will not get in the hot enclosure. The atmosphere excess is vented out of the furnace and lit up at the exit point.
Continuous furnaces are made as tunnels with a preheat zone, a working zone and a cool down zone. Hydrogen furnaces are also called hump furnaces because of their shape. The brazing zone is at the highest point where hydrogen collects. Parts are moved through the furnace on a conveyor.
Vacuum furnaces are widely used in specialized industries requiring utmost cleanliness and exceptional performance. Series of vacuum pumps evacuate the cold wall furnace (the external surfaces are usually kept cold by circulating cooling water). Electrical Brazing-heating is provided by radiating elements.
ANSI/AWS C3.6M/C3.6:2008
Specification for Furnace Brazing
Edition: 3rd
American Welding Society, 12-Sep-2007, 28 pages
An Article on Brazing in an uncleaned vacuum furnace was published (3) in Issue 135 of Practical Welding Letter for November 2014.
Click on PWL#135 to see it.
An Article on Filler Metal for Aluminum Brazing [in vacuum] was published (4) in Issue 139 of Practical Welding Letter for March 2015.
Click on PWL#139 to see it.
An Article on Measuring Heating Rates in Vacuum Furnaces was published (3) in Issue 140 of Practical Welding Letter for April 2015.
Click on PWL#140 to see it.
An Article on How to get dry Gas at the Brazing Furnace was published (3) in Issue 141 of Practical Welding Letter for May 2015.
Click on PWL#141 to see it.
An Article on Filler Metal for Vacuum Furnace Brazing of superconducting radiofrequency cavities was published (4) in Issue 145 of Practical Welding Letter for September 2015.
Click on PWL#145.
An Article on Furnace Brazing Carbon Steel was published (3) in Issue 147 of Practical Welding Letter for November 2015.
Click on PWL#147.
An Article on Aim for Small, Concave Braze Fillets was published (3) in Issue 148 of Practical Welding Letter for December 2015.
Click on PWL#148.
An Article on Brazing Titanium was published (3) in Issue 151 of Practical Welding Letter for March 2016.
Click on PWL#151.
An Article on Sinter Brazing was published (3) in Issue 166 of Practical Welding Letter for June 2017.
Click on PWL#166.
To get at no cost every issue of PWL as it is published, please subscribe.
Dip Brazing
This method consists in applying Brazing-heating by immersing the solid parts either in a molten flux or in molten metal, in a bath kept at suitable temperature. A metallic bath, covered with a flux, provides the molten filler metal. The cleaned parts should be covered with flux at the joint locations. Buoyancy must be taken into account when fixturing.
This is a most effective method of applying heat uniformly and rapidly by direct contact. It is used especially for aluminum parts where the filler metal may be provided as a thin layer clad on aluminum sheet (called brazing sheet) from which parts are formed.
Preheating may be needed especially for massive parts to avoid flux freezing on the cold parts or to dry parts if there is risk of humidity being trapped on them. After brazing, the flux must be removed while parts are still hot.
Induction Brazing
Brazing-heating can be applied by induction, by making the part a shorted circuit secondary winding of a transformer of which the water cooled induction coil is a primary, carrying alternating current. The assembly to be brazed is not part of the electric circuit.
Brazing-heating is generated by the resistance to the flow of the induced current in the part. Knowledge is required to design effective coils. If the induction coupling is effective, heating to temperature is reached in a matter of seconds.
Assemblies ready to be processed should include filler metal already put in place and also flux, unless brazing is performed in a protective atmosphere.
For mass production, machines can be built, capable of presenting assemblies to the brazing coil in rapid succession.
ANSI/AWS C3.5M/C3.5:2007
Specification for Induction Brazing
Edition: 2nd
American Welding Society, 24-Aug-2007, 26 pages
An Article on Controlled-Atmosphere Induction Brazing was published (7) in Issue 136 of Practical Welding Letter for December 2014.
Click on PWL#136 to see it.
Resistance Brazing
If the assemblies to be brazed are part of the electric circuit and Brazing-heating is generated by resistance to the flow of applied current, then this brazing method is called Resistance Brazing.
Current is applied through water cooled electrodes connected to a transformer. A Resistance Brazing Machine can be made by adapting a spot welder to this application. Suitable pressure must be applied to assure contact between the electrodes and the assembly to be brazed.
In many applications the heat is generated at the electrodes. It flows into the assembly, preferably simple and uniform, permitting brazing. Components should be free to move unconstrained even if they expand as heated.
Flux is applied on cleaned parts, immediately before brazing, as wet, conductive slurry to the joint, unless a protective atmosphere is preferred, together with the filler metal.
Diffusion Brazing
Diffusion Brazing is similar to conventional Brazing in that a fusible filler metal undergoes melting to promote the joining of two or more members. A significant difference is however that Capillarity may or may not be used for driving the molten filler metal into the brazing joint clearance.
In this process however, the filler metal has a composition very similar to that of the base metals, but includes melting temperature depressants that cause its melting at a temperature that does not affect the base metal.
This is the case for example of nickel where small additions of silicon or boron lower the melting point of the filler metal, so that it melts and wets the base metal at the brazing temperature. The depressants then diffuse out of the joint.
At that point the change of composition causes the brazing filler to solidify. The temperature is maintained for quite longer a time to promote homogenization, so that in the end the joint line (in a section) may be indistinguishable from the unaffected material. This process is also called Transient Liquid-phase brazing.
In a slightly different method, the filler metal is of such a composition that it forms with the base metal a low melting alloy (called eutectic) that melts right in the joint. An example is that of titanium that forms eutectic with copper at a temperature lower than the copper melting point.
Here the diffusion stage, that can last even a few hours, at variance from the diffusion welding process (see Diffusion Welding) is needed to obtain homogeneous structure and properties, once the joining is already completed.
Brazing filler metals may be similar to those used for regular brazing, if they are chosen so that diffusion will alter their composition once joining is performed. As such they should meet the requirements of AWS Specification A5.8 or equivalent. They can be in the form of powder, foil or wire, usually ready to use for the given joints as preforms.
Occasionally the Brazing-heating cycle is combined with heat treatments as needed. The brazed joint should develop mechanical properties as good or better than those of the base metal.
[Note: This section is copied from (4) "Filler Metals for Diffusion Brazing" published in Issue 53 of our Practical Welding Letter for January 2008. Click on PWL#053 to see it.]
Infrared Brazing
Brazing-heating can be applied by quartz lamps that emit invisible infrared radiation at high power levels. Reflectors may be used to concentrate the radiation on the parts.
Depending on requirements, brazing may be performed in vacuum or in inert gas at lower than atmospheric pressure. Cooling platens (heat pumps) may be used to dissipate excess heat after brazing is completed.
Conclusion
Depending on technological and production requirements, economical methods of Brazing-heating may be applied by selecting the most appropriate way to melt brazing filler metal and have it flow in the joint to provide brazements meeting design requirements.
Watch the following Video on
Induction Heat Brazing
https://www.youtube.com/watch?v=vST78zUWHiU |
* * *
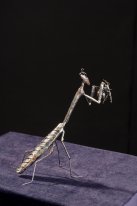
Insect
[From https://www.welding-advisers.com/images/nature-21438478.jpg]
Any questions or comments or feedback? Write them down and send them to us by e-mail.
Click on the Contact Us button in the NavBar at top left of every page.
If you did not yet find what you need, why not typing your question in the following Search Box?
Let us remind you that, if you are interested, we offer a no cost subscription to our Practical Welding Letter and a bonus book in pdf format to be made available for download to your computer on the subject of
PRACTICAL HARDNESS TESTING MADE SIMPLE. Click on Subscription.
To reach a Guide to the collection of the most important Articles from Past Issues of Practical Welding Letter, click on Welding Topics.
Back Home
PROCESSES
Site Map
Brazing
Brazing Joint Design
Brazing Aluminum
Brazing Copper
Brazing Stainless Steel
Brazing Cast Iron
Brazing Titanium
Brazing Ceramic
Brazing Steel
Brazing Nickel
Brazing Magnesium
Brazing Beryllium
Brazing Graphite
Brazing Inspection
Brazing-heating Top
Watch the following Video...
Click on the following image to watch the SBI! TV Show!
POWERED BY:
Click on this Logo NOW!
Copyright (©) 2008, 2009, 2010, 2011, 2012, 2013, 2014, 2015, 2016, 2017
by Elia E. Levi and www.welding-advisers.com
All Rights Reserved