Mig-welding-tips:
do you master them all?
SOLUTIONS with Effective, Powerful Advice
Mig Welding Tips for Mastering the Process
|
Welding Problem? Solve it! with
Help from a Welding Professional Contact Us.
|
Note: To view Google Ads, Pls.
Right Click and Open in a New Window.
|
Mig-welding-tips presented hereafter review important aspects and point to special features of this popular process.
Officially it is designated as GMAW - Gas Metal Arc Welding.
The still popular name MIG (Metal Inert Gas) was initially adopted when the inert gases used to weld aluminum were only argon or helium.
Later on, mixtures of active gases like oxygen, hydrogen and carbon dioxide to weld other metals were introduced.
Therefore the word inert was dropped from the description, with the adoption of the accepted new name.
For basic information on the physics of electric arc for welding, see our new page on Arc Welding.
|
Mig-welding-tips should be universally known, being the process quite diffused, widely popular and successful in numerous applications.
It is contended however, by no less authority than Ed Craig, a universally acclaimed renowned world expert, that unfortunately many misconceptions still limit its use.
Ed is the author of the fundamental book A Management and Engineers Guide to Mig Welding, Quality-Costs-Training.
The book is available from www.weldreality.com
One of the most damaging errors is letting welders do it their way, even if they, despite the considerable skill they may have in stick (Shielded Metal Arc) welding, ignore basic Mig-welding-tips.
In particular it seems that no coordinated effort is dedicated by those in charge, mainly managers and welding engineers, to educate designers to make the best use of the process.
Also no training of welders is performed, to provide them with Mig-welding-tips on how to select their parameters to improve quality and reduce costs.
Mig-welding-tips and progress with Pulse Waveforms
We hope that these Mig-welding-tips will spur renewed interest in the principles of this process.
This should bring about a review of practical applications, to check if they are performed in an effective and economic way.
GMAW uses a continuous, consumable electrode wire, fed from a spool, to provide the needed filler metal.
A welding arc is established between electrode and work with energy drawn from a suitable power supply.
Shielding of hot and molten metal is provided by a protective gas flowing from proper containers.
The Gas Metal Arc Welding (GMAW) process provides the following main Advantages:
- It is compatible with all commercial metals
- Continuous welding is done by pulling electrode wire from a spool
- Welding can be performed in all positions
- Weld deposition rate can be pushed higher than that from alternative processes
- Economics are favorably influenced by higher welding speed
- Versatility of performance permits adapting to wide varying conditions
- Post weld cleaning is reduced to minimum
- Manipulation skills are easily learned and mastered by apprentices
- The process is easily adapted to mechanized or robotic applications
Among all important Mig-welding-tips one should remember that the Limitations are:
- Equipment is more complex and expensive than that of alternative processes
- Hard to reach locations are less easily welded because of bulky torch and cables
- Wind or air drafts may compromise gas shielding
- Reactive metals (i.e. titanium) may need special shielding provisions
- High heat may be uncomfortable to welders
- Correct parameter selection learning needs dedicated training
The first of our Mig-welding-tips reminds that most of Gas Metal Arc Welding (GMAW) applications are performed with direct current reverse polarity (electrode positive) from constant voltage (CV) power supplies.
Only if shallow penetration is required (i.e. for weld surfacing and cladding) straight polarity (electrode negative) can be used.
Once started with correct parameters the process is self regulating.
A built in feature is designed to keep the arc length constant despite minor changes in the distance between the hand held torch and the work, as explained hereafter.
With constant current (CC) power supplies, the wire feed speed is regulated by the voltage measured by a sensor across the arc.
A rise in voltage caused by an occasional longer arc due to increased torch distance causes the wire feeder to increase the wire speed, thus reducing length and voltage to the previous condition.
With constant voltage (CV) power supplies, the current is determined by the wire preselected constant feed speed. Arc length and wire melt-off rate are in equilibrium.
An occasional longer arc due to increased torch distance causes a current drop, due to increased electrode extension (see hereafter), that limits the wire melt-off.
More wire is thus available to shorten the arc length because of the constant wire feed. Current is then increased and a new equilibrium is reached at the previous arc length.
One of the all important Mig-welding-tips, the essence and function of the electrode extension (also called electrode stick-out) should be reminded here.
It is the length of electrode in the torch between the sliding electrical contact and the arc. It has to be set as needed before starting the job by choosing the proper voltage, but it may change as the torch to work position changes.
The total current supplied in the welding operation is partitioned between two competing processes.
The current flowing in the wire between the contact and the arc, contributes to heat that length of wire.
This is due to resistance heating at least with steel, not with aluminum, (because of lower electrical resistance) and prepares its tip to melt more easily.
The remaining amount of current is used up to feed the arc.
It is the arc current that determines weld penetration and deposition rate.
Higher current causes more electrode melting and larger and more fluid weld pools. This may complicate or prevent welding in vertical or in overhead position.
There is close relationship between electrode diameter and optimum current to obtain a well defined bead shape.
Gas Metal Arc Welding (GMAW) provides the unique capability to establish the metal transfer mode adapted to the application.
This is done by selecting properly the most controlling factors following proper Mig-welding-tips:
- Type, intensity and polarity of welding current
- Electrode size
- Electrode composition
- Electrode extension
- Shielding gas mix composition
The first and the last of the above Mig-welding-tips are those most often considered.
An Article on Shielding Gases (7) was published in Issue 48 of Practical Welding Letter for August 2007. Click on PWL#048 to see it.
Note: To view Google Ads, Please
Right Click and Open in a New Window.
|
Short Circuit Arc Transfer Mode
This low heat input mode, producing a small, fast freezing weld pool, is best applied to weld thin materials.
It works in any position, as suggested by widely known Mig-welding-tips, even for relatively large joint gaps.
It uses the lowest practical ranges of current and small electrode sizes.
It consists in a rapid succession of short circuits generated when the wire tip contacts the work. Metal is transferred in the form of small drops.
Although current is lower than with other modes, a great influence is played by the gas mix used. Excessive voltage will cause objectionable spatter.
Globular Transfer Mode
This type of transfer mode, occurring at higher currents, should be avoided in all positions except possibly the flat one.
The reason is because it is difficult to manage. Large drops are formed, pulled down by gravity. Spatter is difficult to control.
Spray Transfer Mode
For thicker sections, at higher than the so called "spray transition current", this mode provides high deposition rate and substantial penetration
A spatter free stream of axially directed small drops permitting welding in all positions.
Pulsed Arc Transfer Mode
Consider the following Mig-welding-tips. Maybe a different type of Power Supply will make a big difference for your fine Jobs?
Special power supplies allow the current to follow a specific pattern whereby upon a background low level that keeps the arc but does not melt metal, pulses of a higher level current are superposed that melt filler wire drops.
This low heat input mode, called GMAW-P for pulsed, permits to provide the advantages of spray transfer mode to thin sections.
It reduces the average current level to an acceptable level that does not cause burn through.
Different versions exist of this basic principle, contributing to over choice confusion.
It is often selected even for application that could be dealt with by using a standard approach.
This one may be one of the most important Mig-welding-tips.
Given the substantial equipment cost difference, it would always pay to check first if the given job can be welded with regular equipment.
Note the following Mig-welding-tips: two additional features available sometimes in equipment should need some attention.
Slope Control
With reference to the standard graph expressing the relationship between current and voltage.
Constant Voltage power supplies would present a horizontal line or one of a limited slope down. This would be adequate for high current density and for Spray Arc.
When using small size wires and low currents, however, that is for Short Circuit Transfer Mode, there is a need to limit the amount of short-circuit current that the power supply can deliver.
A high short-circuit current generates a powerful "pinch-effect" or magnetic squeezing force that separates violently the molten drop from the wire.
If the short-circuit current is limited to a moderate value, by selecting a suitable slope, the detachment will be smooth with no or little spatter.
Note that if the slope is too steep, the current will be too low, and the unmelted electrode will stick to the work.
Variable Inductance
Inductance control regulates the time rate of current change in response to changes in the circuit.
Adding some more inductance may prove beneficial in developing a more stable arc initiation.
One of the Mig-welding-tips that can have practical influence is the following.
In Short Circuit Transfer Mode inductance limits the pinch effect, which will be applied more gradually, by controlling the rate of current rise in time.
Higher inductance will decrease the number of short-circuits per second. The weld pool will become more fluid, resulting in smoother, flatter weld bead.
Too much inductance however will negatively affect arc initiation.
In Spray Transfer Mode, more inductance will only affect arc starts, which will result softer. No influence will be detected once the arc is running.
Additional information and Mig-welding-tips on the principles governing parameter selection for GMAW has been presented in four consecutive issues of our Practical Welding Letter.
You can see them by clicking on the following links:
PWL#023
PWL#024
PWL#025
PWL#026.
An introduction to a website page on Electrogas Welding was published (8) in Issue 82 of Practical Welding Letter for June 2010.
Click on PWL#082 to see it.
The following documents include information essential to the subjects dealt with in this page on Mig-welding-tips.
Recommended Practices for Gas Metal Arc Welding
Document Number: ANSI/AWS C5.6-89(R1994)
American Welding Society / 16-Aug-1989 / 65 pages
Recommended Practices for Shielding Gases for Welding and Plasma Arc Cutting
Document Number: ANSI/AWS C5.10/C5.10M-2003
American Welding Society / 01-Jan-2003 / 72 pages
Specification for Carbon Steel Electrodes and Rods for Gas Shielded Arc Welding
Document Number: AWS A5.18/A5.18M:2005
American Welding Society
01-Jan-2005
Standard Welding Procedure Specification (SWPS) for Gas Metal Arc Welding (Short Circuiting Transfer Mode) of Galvanized Steel (M-1), 18 through 10 Gauge, in the As-Welded Condition, with or without Backing
American Welding Society
Document Number: AWS B2.1-1-003:2002
01-Jan-2002
Standard Welding Procedure Specification (SWPS) for Gas Metal Arc Welding (Short Circuiting Transfer Mode) of Carbon Steel to Austenitic Stainless Steel (M-1 to M-8, P-8, or S-8), 18 through 10 Gauge, in the As-Welded Condition, with or without Backing
American Welding Society
Document Number: AWS B2.1-1/8-006:2002
Get the most important and useful Guide to GMAW:
"A Management & Engineers Guide To MIG - Flux Cored
Weld Quality - Productivity and Costs"
Written by Ed Craig. (Over 600 pages). Available from
http://www.weldreality.com/eds_training_materials.htm#mig
See Hybrid Welding.
An Article on Process Extensions of GMAW was published in section 2 of the issue 30 of Practical Welding Letter for February 2006. To see the article click on PWL#030.
An Article on Pulsed GMAW (GMAW-P) was published in section (2) of issue 76 of Practical Welding Letter for December 2009. To see the article click on PWL#076.
A Mid Month Bulletin was published on September 15, 2008 with Resources on Laser-Arc Hybrid Welding.
Click on PWL#061B to download it.
An Article on Ultrasonic Force Assisted Metal Transfer in GMAW was published in section (7) of issue 104 of Practical Welding Letter for April 2012. To see the article click on PWL#104.
An Article on Improving GMAW performance was published (2) in Issue 105 of Practical Welding Letter for May 2012.
Click on PWL#105 to see it.
An Article on Selecting and Maintaining GMAW Torches was published (3) in Issue 117 of Practical Welding Letter for May 2013.
Click on PWL#117 to see it.
An Article on Pulse Welding Control Systems was published (7) in Issue 132 of Practical Welding Letter for August 2014.
Click on PWL#132 to see it.
An Article on Improving GMAW Efficiency was published (2)
in Issue 137 of Practical Welding Letter for January 2015.
Click on PWL#137 to see it.
An Article on Hybrid Induction Arc Welding was published (2) in Issue 138 of Practical Welding Letter for February 2015.
Click on PWL#138 to see it.
A new page on Robotic Arc Welding (Opens a new page) was recently added to this website. It deals with applications of GMAW for increased productivity.
An Article on A New, Rotating Arc Welding Technology was published (4) in Issue 143 of Practical Welding Letter for July 2015.
Click on PWL#143 to see it.
An Article on Optimizing Robotic Welding with the Right GMAW Gun and another one on GMAW Gun Troubleshooting were published (2)(3) in Issue 145 of Practical Welding Letter for September 2015.
Click on PWL#145.
An Article on Remote Control Welding Technologies was published (3) in Issue 149 of Practical Welding Letter for January 2016.
Click on PWL#149.
An Article on Metal Cored Filler Wire was published (4) in Issue 153 of Practical Welding Letter for May 2016.
Click on PWL#153.
An Article on Advances in GMAW Power Sources was published (7) in Issue 154 of Practical Welding Letter for June 2016.
Click on PWL#154.
An Article on Feedability of Aluminum Filler Metal in GMAW was published (3) in Issue 155 of Practical Welding Letter for July 2016.
Click on PWL#155.
An Article on Spatter Reduction was published (3) in Issue 158 of Practical Welding Letter for October 2016.
Click on PWL#158.
An Article on Tips on GMAW Guns was published (2) in Issue 162 of Practical Welding Letter for February 2017.
Click on PWL#162.
An Article on Pulsed GMAW was published (3) in Issue 163 of Practical Welding Letter for March 2017.
Click on PWL#163.
An Article on Monitoring GMAW was published (11) in Issue 165 of Practical Welding Letter for May 2017.
Click on PWL#165.
An Article on A Study on argon/hydrogen blend was published (11) in Issue 169 of Practical Welding Letter for September 2017.
Click on PWL#169.
Click on My Store to find a few MIG Welding Sources you may like.
NEW RESOURCES
Find some interesting links in a special Mid Month Bulletin Page of our PRACTICAL WELDING LETTER, designed to offer you, our interested readers, the opportunity to search the web quickly and effectively on the subject of Gas Metal Arc Welding (MIG). We urge you to explore this rich source of essential knowledge. Online Resources on Gas Metal Arc Welding (MIG), presenting Guide, Guidelines, Handbook, Troubleshooting, Downloads, Video, Simulation, Hybrid and Information is now available by clicking on PWL#056B. |
Do you need more Resources?
Click on the Weld Resources Button on the Navigation Bar at Top Left of this page.
Watch the following Video on
GMAW MIG Welding
https://www.youtube.com/watch?v=5mcTl0VrvWQ |
* * *
Any specific questions or comments? Write them down and send them to us by e-mail, by a click on Your Questions and Feedback. We plan to update this Mig-welding-tips page following readers' input
* * *
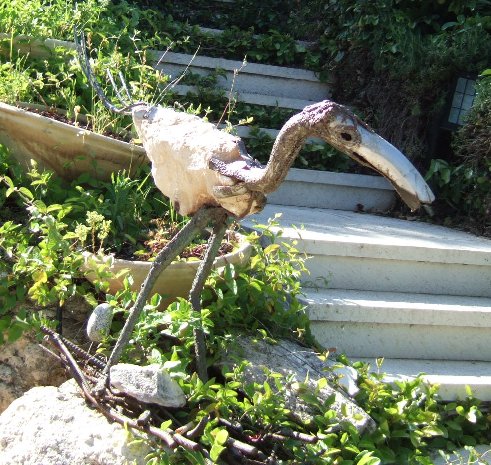
Bird by Uri Sharon
[From https://www.welding-advisers.com/Hobby-welding.html]
Let us remind you that, if you are interested, we offer a no cost subscription to our Practical Welding Letter and a bonus book in pdf format to be made available for download to your computer on the subject of
PRACTICAL HARDNESS TESTING MADE SIMPLE. Click on Subscription.
To reach a Guide to the collection of the most important Articles from Past Issues of Practical Welding Letter, click on Welding Topics.
Note: To view Google Ads, Please
Right Click and Open in a New Window.
|
Back HOME
Back to PROCESSES
Back to Site Map
Tig Welding Tips
Plasma Welding Tips
Flux Cored Arc Welding Tips
Submerged Arc Welding Tips
Shielded Metal Arc Welding Tips
Oxyacetylene Welding Tips
Vertical Welding Tips
Resistance Welding Tips
Pipe and Tube Welding
Welding Underwater Processes
Brazing
Brazing Joint Design
Brazing Heating
Braze Welding
Resistance Brazing
Soldering
Wave Soldering
If you did not yet find what you need, why not typing your question in the following Search Box?
Mig-welding-tips Top
How could you start an Online Business?
Watch the video...
What's stopping YOU from trying SBI!?
Click on the following image to watch the SBI! TV Show!
POWERED BY:
Click on this Logo NOW!
Copyright (c) 2006, 2007, 2008, 2009, 2010, 2011, 2012, 2013, 2014, 2015, 2016, 2017
by Elia E. Levi and welding-advisers.com
All Rights Reserved
Mig-welding-tips on fundamental properties and characteristics of GMAW can establish your reputation as an expert, and contribute largely to your successful applications.