Soldering
may be the right answer
Solutions with Effective, Powerful Advice
Welding Problem? Solve it! with
Help from a Welding Professional Contact Us.
|
Note: To view Google Ads, Pls.
Right Click and Open in a New Window.
|
What are these Soldering processes?
When are they preferred to other joining methods?
What is critical to their successful application?
We would like to propose in the following some of the most important aspects of these processes.
They provide effective and economical solutions for a wide range of common joining problems.
The definition describes a joining process of metallic objects where coalescence or attachment is obtained by heating to a suitable low temperature, usually below 450 °C (840 °F).
The process uses nonferrous filler alloys (solders) which melt at temperatures lower than that of the base materials to be joined.
Capillary attraction helps in spreading the solder between the properly fitted surfaces.
What is in here for me?
If you did not yet find what you need, why not typing your question in the following Search Box?
One of the oldest processes for fastening together different metals is Joining by solder.
It is still applied in modern times to join metals with a low temperature melting filler.
Certain special, important niches in industrial applications, use it with due improvements and advancements.
Older people may still remember the time before the ubiquitous introduction of plastic containers and implements.
During that age many household items were mostly handmade by a myriad of individual artisans, either working for themselves or grouped in factories.
They used to cut by scissors thin sheets of tin or zinc plated steel, or of lead or zinc.
They formed them in useful shapes by simple tools.
And then they soldered them at the overlapping edges with a solder alloy, using a low temperature manual torch or heated copper tools.
In more modern times virtually all electrical connections were manually performed by this process with a hand held heated copper tool (usually called a soldering-iron).
That was the process used mainly in the in appliances and radio sets industry.
Later, the appearance of PCB (Printed Circuit Boards) promoted the development of automated processes.
These included mostly Wave-soldering of boards, with molten solder performing many joints at once.
See further down the link to a new page on this process.
An essential element of the process is the use of flux.
It is required to clean the surfaces from objectionable oxide or other disturbing layers.
Cleanliness allows wetting and metallurgical bond between solder and base material.
Bond
The nature of the junction is more than adhesion or mechanical attachment, although these contribute to strength.
It is rather a metallurgical bond at the atomic level, produced at the filler-metal/substrate interface.
This property is essential when the purpose of this process is to provide electrical conductance and continuity of circuit functionality.
Advantages
The flow and wetting properties of correctly applied solder, permit the joint to be performed in place by itself, without precisely directing the heat source to the connection place.
The low temperature means that no damages are generated in other elements, permitting a large selection of design items and dimensions.
Joints can easily be disassembled permitting modifications or repair.
The equipment is relatively simple and the process can be automated for mass production.
Joint Design
Quite usually, the actual joint shape to be selected depends mostly on application, on base metal and on service conditions.
As solders are intrinsically weak, strength is seldom a requirement.
Joints are designed so that the strength requirements are fulfilled by interlocking elements.
The solder function is limited to sealing or stiffening, to avoid physical separation or to ensure electrical continuity.
Integral with design is the compatible heating process to be employed and the method of introduction of flux and of solder in the joint.
This means that both heating method and solder form and application must be specified on drawings or production sheets.
For sheet metal, overlapping edges are preferred, possibly interlocked.
Wires are usually tinned and interwoven before joining.
If possible, solder should be applied from one side on the joint, as its appearance at the other side after soldering is a proof of spread along all the area.
This is particularly useful for fitting on tube soldered joints.
Precleaning
A most important operation to be performed before soldering, precleaning is an essential element to the success of this joining process.
All foreign materials like oil, grease, paint, dirt, auxiliary production lubricants, marker traces etc. will interfere with proper surface wetting and solder flowing.
That could impair the quality or make soldering utterly impossible.
Therefore, depending on the conditions of the surfaces, one or more of the following methods must be planned into the work plan, to ensure the best preliminary conditions.
Degreasing, scrubbing, mechanical abrasion and even acid or alkaline cleaning for removal of most adherent rust or oxides are among the processes used.
Even rinsing water should be treated, if necessary, because residues from hard water may interfere with the process.
Precoating
In certain cases, for difficult to join metals, one should consider precoating (tinning) with a more easily soldered alloy.
By this method the use of strong acids during soldering could be avoided, as all residual traces can be rinsed away after precoating.
Acid residuals may be difficult to remove from soldered joints and could be a cause of corrosion if not removed thoroughly.
Fluxes
The fluxing action consists in the removal of thin oxide layers or other interfering impurities from the surfaces undergoing soldering.
That permits intimate contact and wetting of the base metal by the molten solder alloy, through reduction of its surface tension.
Fluxes are displaced by the molten solder, and any residues should either be non corrosive, or should be thoroughly eliminated.
Fluxes may be applied in form of liquids, pastes or even gaseous materials.
In automatic soldering-machines, liquid flux is applied by spraying, just before immersion of boards in the molten solder.
Fluxes may be noncorrosive, mild, intermediate or highly corrosive depending on base materials and their condition.
Fluxes are sometimes in the form of natural occurring resins.
These perform well for the soldering-process except that they tend to produce fumes, called colophony, which can be irritant or produce allergic reactions.
New resin free fluxes are being proposed and available.
Mass production
Automatic-soldering by wave-, drag-, or dip machines is a successful method for making high-quality, reliable joints.
If correctly controlled, this is one of the least expensive methods for mass fabricating electrical connections.
Machines performing joining under a blanket of inert nitrogen gas produce less oxidation (dross) in the molten material.
The claimed advantage is requiring less maintenance, cleaning and solder usage.
Solder alloys
Note: To view Google Ads, Please
Right Click and Open in a New Window.
|
Selection of a certain solder is based on its
melting properties, which depend on its composition, expressed as melting range (Solidus - Liquidus interval) and the temperature conditions in service.
Only pure metals and eutectic alloys present a single melting point.
Tin-lead solders have been most popular in the past and are still in wide use.
New applications require the use of materials friendly to the environment.
Lead is considered poisonous and therefore it is now banned from many industries.
Efforts were exerted to remove the chance that lead based residuals find their way to the environment because of negligent production procedures.
Due to the wide range of properties deriving from compositions, these alloys are used in many industrial applications, from plumbing, radiators, electrical and electronic connections.
The most popular composition for electronic applications used to be the eutectic alloy of 63% tin (Sn) and 37% lead (Pb), which melts at 183 °C. It is now almost completely excluded from industrial applications.
Specifications set the maximum of impurities in solders, as it was determined that they can impair performance characteristics, like wetting, flow, temperature, strength and oxidation resistance.
Elements like Aluminum, Antimony, Arsenic, Bismuth, Cadmium, Copper, Iron, Nickel, Phosphorus, Sulfur, and Zinc, even if within limits in the original filler, tend to increase in the mass of solder during normal use.
When used as main constituents, not as unwanted impurities, Antimony, Silver, Zinc, Indium, Bismuth, and Cadmium alloyed with Tin provide classes of solders of special characteristics, like low temperature.
Precious metal solders, based on Gold find specialized applications.
Environment friendly solder materials
There has been a growing concern over the continued use of lead in currently used solders, particularly for the electronic industry.
Sample pages of a thorough study on the influence of lead containing solders and on other dangers to the environment can be found in
http://www.elchempub.com/samples/Hwang.pdf
An Article on a New Lead-free Solder Alloy was published in Issue 42 of Practical Welding Letter for February 2007. Click on PWL#042 to read it.
To receive every issue of Practical Welding Letter as it is issued, please Subscribe.
Some authors contest this being a real problem, or call it a nonproblem, because in their view it is not proven that lead containing solders pose a threat to the environment.
While the scientific proof for need of lead-free soldering may be questionable, consumer and legislative requirements for its production are not.
The fact is that a mounting drive pushes towards a new class of solders containing no lead.
The switch is not without problems. For one thing, the new solders melt at a temperature higher by 30 to 40 °C to that of lead containing solders.
This change alone requires a complete redesign of the applications, involving reevaluation of flux, cleaner, substrate, finish and packaging processes.
Specifications
Specifications and standards have established requirements for certain solder alloys in terms of composition limits, impurity levels, and a nomenclature for referencing particular compositions.
In the United States, the specifications of solder alloy compositions are listed in ASTM B 32. In Europe the International Organization for Standardization (ISO) issued the specification ISO/DIS 9453.
In conclusion soldering is a mature process for joining a definite class of items, especially for electrical circuits containing different elements.
Automated machines and procedures are available which permit low cost production with high reliability of performance.
The following Documents are relevant to the subject treated.
ASTM B32-08
Standard Specification for Solder Metal
ASTM International / 01-May-2008 / 9 pages
AWS SHB
Soldering Handbook
Edition: 3rd
American Welding Society, 01-Jan-2000, 577 pages
See the new website page on Wave Soldering.
A short note on resources for Lead Free Solder Filler Metals was published (4) in Issue 74 of Practical Welding Letter for October 2009. Click on PWL#074 to see it.
An Article on Filler Metals for Active Solder Joining was published (4) in Issue 75 of Practical Welding Letter for October 2009.
Click on PWL#075 to see it.
An Article on Substitution of lead based solders was published (3) in Issue 101 of Practical Welding Letter for January 2012.
Click on PWL#101 to see it.
An Article on Acoustic Imaging for process quality control was published (3) in Issue 143 of Practical Welding Letter for July 2015.
Click on PWL#143 to see it.
An Article on A new metallic glue was published (11) in Issue 150 of Practical Welding Letter for February 2016.
Click on PWL#150.
An Article on Reliability of Soldered Joints was published (4) in Issue 164 of Practical Welding Letter for April 2017.
Click on PWL#164.
On Soldering Safety see at page 45
http://www.aws.org/technical/AWS_Z49.pdf
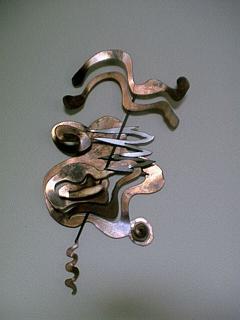
Artwork for Hobby
[From https://www.welding-advisers.com/artwork-for-hobby.html]
Watch the following Video on
How to Do It: Basic Soldering
https://www.youtube.com/watch?v=BLfXXRfRIzY
|
* * *
Any questions or comments or feedback? Write them down and send them to us by e-mail.
Click on the Contact Us button in the NavBar at top left of every page.
Let us remind you that, if you are interested, we offer a FREE subscription to our Practical Welding Letter and a FREE book in pdf format to download to your computer on PRACTICAL HARDNESS TESTING MADE SIMPLE.
Click on Subscription.
To reach a Guide to the collection of the most important Articles from Past Issues of Practical Welding Letter, click on
Welding Topics.
Note: To view Google Ads, Please
Right Click and Open in a New Window.
|
Back
Home
Processes
Site Map
Friction Welding Processes
Friction Stir Welding
Friction Surfacing
Flash Welding Process
Stud Welding
Upset Welding
Resistance Welding Processes
High Frequency Resistance Welding
Projection Welding
Gas Welding Processes
Arc Welding Processes
High Energy Welding Processes
Laser Drilling
Micro Welding Processes
Soldering Top
Watch the following Video
POWERED BY:
Click on this Logo NOW!
Watch - The Video:
Why Don't I Work From Home?
and also
Think outside the Cube.
Follow this Invitation!
Experience C2 power and flexibility in action by clicking SBI! 2.0 For You. Where SBIers share their business-building experiences first-hand. You will realize that there is nothing comparable to SBI! when you read real stories from SBIers who share how C2 has helped them expand, accelerate, build trust and monetize their sites.
|
Copyright (c) 2004-2012, 2013, 2014, 2015, 2016, 2017
by Elia E. Levi and www.welding-advisers.com
All Rights Reserved
Soldering is a simple and successful process, most useful when properly applied. Read on it here...