Braze-welding
with low heat
Solutions with Effective, Powerful Advice
Useful Alternative Process not to Miss |
Note: To view Google Ads, Pls.
Right Click and Open in a New Window.
|
Braze-welding is a joining process that uses an oxyacetylene flame with standard or portable equipment and mainly copper alloy filler metals.
It provides soft and ductile metal deposit layers, and is used for production assembly and for repair of tools or cast iron items.
It is a low cost substitute for brazing. It can be used for buildup of worn out material.
It is a lower temperature alternative to welding in that it does not melt the base metals.
It provides good strength joints. These and other highlights are presented here for information of interested readers.
Braze-welding Characteristics
This process heats and melts the filler material at a temperature above
450 °C (840 °F) but below the melting temperature of the base materials, does not depend on capillarity for the distribution of the joining material, and provides a metallurgical bond obtained by wetting the surfaces using a suitable flux.
When is it convenient to consider?
Braze-welding is convenient when high heating is not recommended as for joining cast iron or for repairing a broken wrench of hard tool steel.
It is also suitable when the usual brazing configuration (providing a lap joint with a capillary space where filler metal can be drawn in) is not feasible, and when precise fit-up is not practical.
Why is it recommended for certain jobs?
Essentially because it is less expensive to make while providing, in most cases, sufficient strength for the application intended.
The main drawback is the difference in color which in many cases is of no consequence. In fact yellow-red Copper base filler metals stand out as different in color from iron base materials.
In a previous page on Brazing, the process for capillary joints was introduced.
Advantages and limitations were listed, especially those requirements to be fulfilled for obtaining economically acceptable permanently brazed connections.
UPDATED PAGE
See the updated page now including a description of suggested Oxyacetylene Welding and Cutting Outfits suitable for a wide range of practical welding, brazing, braze-welding and cutting needs. Click on Gas Welding Equipment. |
For a selection of modern OXY-Gas Welding Equipment, Torches and Kits, you may wish to have a look at My Store. |
Braze welding is a similar but different process. As already remarked it is more forgiving in joint requirements, as larger gaps are tolerated.
It is suitable for different cases where regular brazing (driven by capillarity) is not feasible or convenient.
Braze-welding: productive and economical
The manual Braze-welding process makes use of the oxyacetylene flame which is known and available in many shops for production and repair jobs of welding and brazing.
By employing copper base filler rods and special fluxes it permits, with some readily acquired skills, to perform useful joining for production or repair.
Braze-welding of cast iron is an attractive alternative to welding as it requires less heat and therefore less time, less distortion and less cracks.
The edges to be joined should be cleaned to the highest degree, possibly by using a cleaning molten salt bath.
If the cast iron was ground for removing gross contamination, the graphite may be smeared on the surface, impairing wetting and brazing.
In this case one should first remove the smear by fast heating the surface with the oxyacetylene flame until dark red in color, and then, after cooling, by wire brushing the joint area.
Preheating of cast iron for Braze-welding, although not always necessary, may be used for improving results.
Depending on the weld size relative to the casting size, there may be a need of thorough preheating to dull red heat, but not over that, because wetting and tinning might become impaired.
This characteristic presents a self adjusting feature. The welder will easily find the most suitable preheating range for Braze-welding, because either at lower or at higher temperature the wetting is found to be more difficult.
Slow cooling after Braze welding is usually recommended by employing suitable insulating materials. Post heat is not required.
The main advantage of Braze-welding is the fact that it requires less heat and by consequence it is faster (better productivity) than gas welding and also less prone to producing distortion.
Joint strength at room temperature is usually adequate for most purposes. Overheat of the base metal should always be avoided.
Disadvantages of Braze-welding are mainly the no-match color of the filler metal alloy, and a possible increased sensitivity to corrosive conditions, because of general lower corrosion resistance of the filler alloy and of galvanic couple.
Strength is found to fall off rapidly with increasing temperatures, so that service temperature of items fabricated or repaired by Braze welding should be limited to 500 °F (260 °C).
Knowing all the alternatives can help you find the best and most economic solution for production or repair problems.
Filler metals usually employed are types of brasses (copper alloys with zinc and other metals) classified in specifications:
ANSI/AWS A5.7/A5.7M-2007
Specification for Copper and Copper-Alloy Bare Welding Rods and Electrodes
American Welding Society, 12-Apr-2007 , 32 pages
ANSI/AWS A5.8M/A5.8:2011
Specification for Filler Metals for Brazing and Braze Welding
Edition: 10th
American Welding Society / 17-Jun-2011 / 62 pages
ANSI/AWS A5.15-90 (R2006)
Specification for Welding Electrodes and Rods for Cast Iron
American Welding Society / 01-Jan-1990 / 10 pages
ISO 3677:1992
Filler Metal for soft Soldering, Brazing and Braze Welding - Designation
International Organization for Standardization / 01-Jun-1992 /
2 pages
BS EN 13347:2002
Copper and copper alloys. Rod and Wire for Welding and Braze Welding
British-Adopted European Standard / 21-Dec-2002 / 20 pages
ANSI/AWS A5.31M/A5.31:2012
Specification for Fluxes for Brazing and Braze Welding
Edition: 2nd
American Welding Society / 17-Feb-2012 / 38 pages
Crack repair by Braze-welding.
For the repair of cracks in cast iron by Braze-welding, the crack should first be dressed to present an included angle of 60°, with a small radius at the bottom.
It is customary and recommended to drill stop holes at the real ends of existing cracks: they will be filled up in the process of Braze-welding the crack. If oil remnants from machining or service are present in the cast iron body, they should be removed by burning at 1400 °F (760 °C) with an oxyacetylene torch.
Then, after cooling down, the groove should be wire brushed to clean all remaining surface contamination. The proper type selection and the correct application of flux is critical to the success of the application.
Preheat should be applied for the purpose of maximizing wetting of the cast iron surface by the filler metal. A root pass is usually deposited, and then the Braze-welding filler is melted in place to build up all the thickness.
An Article reporting on precautions needed when one wishes to perform braze-welding for joining Aluminum to nodular Cast Iron was published in Issue 28 of Practical Welding Letter for December 2005.
To read the article (in Section 11) click on PWL#028.
An Article on Filler Metal for Braze-Welding was published in section 4 of the issue 30 of Practical Welding Letter.
To see the article click on PWL#030.
To receive by e-mail every new issue of Practical Welding Letter as it is published and to obtain the bonus e-book on Practical Hardness Testing Made Simple click on Subscription.
The above exposition has been centered on manual torch Braze-welding using the oxyacetylene flame as this is indeed the most used implementation. For completeness one should add that other fuel gases could be used if convenient, with due attention to the characteristic of the gas employed.
Furthermore one should know that the gas metal arc welding (GMAW) process has been successfully adapted to Braze-welding with low melting temperature copper based electrodes like aluminum bronze and silicon bronze.
By using low heat input settings, the process is advantageous for joining galvanized steel thin sheets and cast iron, with the additional benefit of better corrosion resistance than with carbon steel filler metal.
Conclusion.
It may pay to gain by practice some basic experience with Braze-welding, in order to think of this process when its benefits are most advantageous for a successful application.
Watch this Braze Welding Video on
Fairbanks-Morse 1 1/2 H.P. https://www.youtube.com/watch?v=D8XegYT_A_U
|
If you did not yet find what you need, why not typing your question in the following Search Box?
* * *
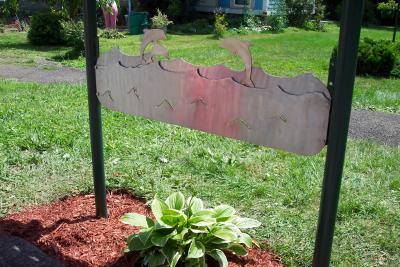
Dolphins In Steel
[From https://www.welding-advisers.com/dolphins-in-steel-mail-box-stand-art.html]
Any questions on Braze-welding or comments or feedback?
Write them down and send them to us by e-mail.
Click on the Contact Us button in the NavBar at top left of every page.
We would like to inform you, just in case you do not know yet, that you are entitled to a no cost subscription to our monthly Practical Welding Letter.
To reach a Guide, listing the most important Articles from Past Issues of Practical Welding Letter, click on
Welding Topics.
And get also a bonus download right to your computer:
our book on
Practical HARDNESS TESTING Made Simple
(in pdf. format).
Just Subscribe to accept it by filling in the form.
Back Home
Site Map
Safety
Friction Welding Processes
Friction Stir Welding
Friction Surfacing
Flash Welding Process
Stud Welding
Upset Welding
Resistance Welding Processes
High Frequency Resistance Welding
Projection Welding
Gas Welding Processes
Arc Welding Processes
High Energy Welding Processes
Braze-welding Top
Would you mind watching a short interview?
It could be most refreshing...
Click on the following image to watch the SBI! TV Show!
POWERED BY:
Click on this Logo NOW!
Copyright (c) 2003-2008, 2009, 2010, 2011, 2012, 2013, 2014, 2015, 2016, 2017 by
Elia E. Levi and
www.welding-advisers.com
All Rights Reserved.
Could Braze-welding be your solution? Find out here by checking what it is, when and how it is used, and what benefits it can provide...