Material-identification
Precondition for Welding
Why is Material-identification so important?
Welding Problem? Solve it! with
Help from a Welding Professional Contact Us.
|
Note: To view Google Ads, Pls.
Right Click and Open in a New Window.
|
What is
Material-identification?
Do you know how to weld your new job?
Sure, provided you know the metals.
But what if you don't? Are you going to guess, to try anyhow? What if it cracks?
Material-identification is necessary, to know what and how you are going to weld.
You should be certain, definitely, if you want to avoid costly surprises.
The most thorough and complete analysis is called sometimes Positive Material Identification.
For repair welding you may not need that. Getting an idea of the family of metals to which the unknown pertains, maybe sufficient to do an acceptable repair work.
It is understood that, most of times, welding involves metals. Plastic materials may need welding too, but that is a completely different job.
You may be given an existing item for repair: in this case you have a physical object to investigate for identifying the metal, before you can write instructions for repair.
Save time and anguish...
It is true that testing the unknown metal to reveal its composition, through Material-identification procedures, will take some time, it may also cost some money.
But by then you will know what you need and you will save a lot of time and of anguish in trying to figure out what to do or what went wrong.
Look more professional...
Tip!: Taking steps to determine the Material-identification of the item in cause looks also more professional and will gain the respect of your customer, who should pay for the tests.
Note: To view Google Ads, Please
Right Click and Open in a New Window.
|
Material-identification is a Must before Welding
Or you may be asked to manufacture a new item, using metals available on the market.
For programmed production, material identification is part of drawing requirements, a well understood engineering responsibility.
Requirements are mostly spelled out in a bill of materials which is intended to specify the materials involved.
If it is complete and professional, no problem.
Old drawings...
But drawings may be written a long time ago, in a distant place, using commercial brand names unknown here and now, or superseded specifications not readily available.
Then the Material-identification offered by the drawing may not be of much help.
We strongly recommend not to spare any effort in trying to obtain full information on the meaning and substance of old notations.
That is because the answer will pay handsomely in saved time, sparing wasted efforts, and... failures.
Otherwise the only other way out is to re-engineer the drawings anew, by taking the usual steps.
A designer employs all his/her professional experience to check all aspects, including functionality, stability, fabricability and economy.
Maybe we can help if you have any questions. Write them down and send them to us by e-mail. Click on the Contact Us button in the NavBar at top left of every page.
One should never be tempted to introduce careless substitution of materials. Even if that could spare a few dimes.
Material selection and substitution is an Engineering function: leave it to those in charge, let them be responsible (in writing).
If you did not yet find what you need, why not typing your question in the following Search Box?
New materials...
It is good practice, and it is recommended when purchasing new material, to obtain Material-identification by requesting a material certificate.
It should include the source or manufacturer's name, material designation and condition, heat number, dimensions, finish, chemical composition, applicable specifications, quantity or weight.
The mechanical properties in a reference condition should be provided (may be different from supply condition), delivery hardness. If something is not clear, ask for explanations.
After collecting regularly these certificates one builds some experience over time.
If you have to change supplier you will know what to request, that gave in the past satisfactory results.
When unexplained differences from the normal are found in the paper, one should inquire, even before trying, if those differences are likely to give variations in the manufacturing and welding processes.
Your vendor would not want to put you in a mess, on the contrary he/she would like to help, if only you tell him/her what you need and what for.
An Article on Receiving Inspection, with more details and practical advice, was published in the January 2004 issue #05 of Practical Welding Letter.
Click on PWL#005 for reading it.
You can subscribe at no cost to our periodic publication by clicking on subscription.
What about repair jobs?...
If you are confronted with a repair item you may not have whom to ask. In this case Material-identification could start with a magnet of the simplest type.
Ferromagnetic materials, like iron and steel, give a strong response, easily determined.
Weak magnetic attraction should not be confused with the previous one: nickel, cobalt and work hardened stainless steel may give some, weak response.
Follow an Identification test procedure
To decide how to weld you must be sure of the metal you are about to join.
If the material is magnetic, it could be either regular steel or magnetic stainless.
To go ahead with Material-identification and find which is which, a simple spot check is suggested.
Put on the cleaned surface of the material (remove oil or grease remnants with acetone) a drop of Nital 5-10% solution (5-10% nitric acid, HNO3, in alcohol or methanol) from an eye drop little bottle.
If there is no reaction the material is probably a stainless.
Otherwise, if it is regular steel, one can see a certain reaction with tiny bubbles, and a dark stain remains on the surface.
Warning: Nital solution has to be prepared only by a knowledgeable chemist, or possibly by a pharmacist.
Nital solution could be dangerous if coming in contact with eyes or skin, it is not to be swallowed, and has to be dealt with by taking appropriate precautions.
The bottle should be marked as dangerous, clearly indicating the content and the date of preparation, and kept out of reach of children.
Then one should check if there is a plating or a surface treatment.
The appearance could tell but only experience will help.
A bright shining layer could indicate chromium or nickel plating.
A drop of 10% copper sulfate (CuSO4) in water would drip away without a trace on a plated steel, while it would leave a bright copper stain on a bare steel surface.
Other quite common plating materials could be zinc or cadmium, usually designed for corrosion protection of mild steel: the nature of the plating should be determined separately.
Condition is important...
Hardness testing comes next for Material-identification. Vickers Hardness is recommended, if a tester is available.
See further down on this page for a book on PRACTICAL HARDNESS TESTING MADE SIMPLE, which is presented FREE for you to download from this Site.
But if you cannot test for hardness, at least you can always try the material with a file: if the file does not take chips, the material is "file hard" and also, probably, hard to weld.
Once you have identified your metal you know all you need about its weldability.
Spark Test
In old times, and possibly even now, manufacturers of grinding wheels used to distribute wall charts for Material-identification. Try to get one from your supplier!
The charts gave a pictorial description of the types of sparks likely to be seen when grinding different types of materials.
Even without a chart you can compare the sparks from the unknown material with those of your known and identified material: if the sparks look different, it is likely that the materials are not the same.
A different test, possibly indicated with the same name, points to a totally unlike trial.
As indicated further down in this page, an analytical optical test called Spark Emission Spectrographic Analysis makes use of precisely emitted sparks in a complex instrument, providing complete compositional analysis.
One should be aware of the difference between the two tests.
Aluminum or Magnesium?...
One can readily distinguish between light alloys like aluminum and magnesium with a simple test, but you should use the help of a chemist.
Aluminum is attacked by caustic soda (NaOH), which is a dangerous material, and also by alkaline solutions, while magnesium is not.
Conversely magnesium is attacked rapidly by usual inorganic acids (excluding hydrofluoric and chromic acid), while aluminum is not attacked by acids like nitric and sulfuric. Also aluminum density is about twice that of magnesium.
Which alloy?...
In the past elaborate differential procedures were used for Material-identification.
These were based on series of "spot checks" with specific solutions prepared for this purpose.
That required that an experienced technician perform numerous attacks in succession, of the material surface.
The decisions were based on reactions and appearance of often not so clearly cut colors on the material or on absorbing paper.
Modern means, described further down this page, render this unreliable and complicate technique obsolete.
The following document provides guidelines for the selection and use of methods suited to the requirements of particular metals sorting or identification problems.
ASTM E1476-04(2010)
Standard Guide for Metals Identification, Grade Verification, and Sorting
ASTM International / 01-Jun-2010 / 13 pages
Copper alloys usually display characteristic colors, but distinguishing among different types of bronze may require the use of XRF test introduced hereafter.
Although Titanium could in principle be determined by its density, which is about sixty percent that of steel, and almost twice that of aluminum, we would suggest to use XRF as a simple and most definitive test.
Most useful test...
The single best and most useful qualitative Material-identification test that we can recommend (although unsuitable for the lightest elements) is called X-Ray Fluorescence (XRF) Spectroscopy.
It is immediate and non destructive, and is performed using special equipment, fixed or portable.
The method consists in exciting the atoms of the elements present in the sample with primary x-ray photons of the required energy.
Excitation means removing certain electrons from the atoms to an unstable (ionized) status.
The relaxation from the excited condition is accompanied by characteristic spontaneous x-ray emission called fluorescence.
As each element has a unique set of known electron energy levels, the x-ray emissions have a well defined energy level for each of the possible electron transitions, providing a "fingerprint" for Material-identification.
The computer analysis of the spectrum of all the collected x-ray emissions (arranged according to their energy or wavelength) permits at least a qualitative Material-identification with various degrees of precision depending on the details of the program used.
For occasional necessities of the welding job shop there is probably no economic justification to procure such equipment.
But this instrument being quite diffused in recent times, you may try to find, through the Yellow Pages or otherwise, a source capable and ready to do the test for you on your sample.
This instrumentation is now common with material suppliers, with service centers, with foundries and even with scrap-yards (where it is used for Material-identification to segregate different kinds of scrap).
Anyone with the instrument could perform the test for you at no cost or at a nominal fee. If you are working for customers, they should bear the cost of this inexpensive test, that any metallurgical laboratory could probably carry out.
We should explain, for completeness, that there exist more elaborate instruments, exploiting the same XRF principle.
These are designed to provide a quite precise quantitative and more costly material analysis report, based on the comparative analysis of known and certified reference samples.
If a laboratory requests a substantial expense, it is probably proposing a more complete and expensive test, like the one above or those indicated hereafter.
It may be nice to have, if you prefer, but you probably do not need it for a first orientation, for welding purposes.
Tip!: if you ask a laboratory to submit to you an offer for the Material-identification of an unknown sample, you can ask to know, besides the cost, which type of test they are proposing, and which test report you will receive from them.
And you should tell them in advance for which purpose you are doing the test. Chances are you will find the answer that fits you best at the least cost.
Complete tests... not always required
If you request more definitive and precise analyses for Material-identification, those can be performed by well equipped laboratories using Spark Optical Emission Spectrography (OES).
In alternative you can ask for quantitative Chemical Analysis (called by interesting names like AAS or ICP).
These are however costly and specialized tests which are rarely required for routine welding, except if incurring in unexpected difficulties.
Summing up, even if one cannot identify through Material-identification procedures the exact composition of an unknown item to be welded, even incomplete information may be enough.
Knowing to which family of metals it belongs and what hardness it presents should be sufficient to devise the best procedure to be applied with the welding process available.
It is strongly recommended to make a welding trial on a scrap and to test it to destruction, to reveal any problems, before tackling the job itself.
It is obvious that in case of failure of the test, the Material-identification should be pushed further and the reasons for lack of success should be determined before starting production.
Further tests...
Many other tests are available to determine the Material-identification of metal samples. Some are mentioned in the ASTM Guide mentioned above.
One quite simple but most useful (acceptance) test consists in performing on a small specimen the usual heat treatment (mostly hardening and tempering if it is steel) and then checking the hardness obtained.
If the result is not what it should be, the material is probably different from what presumed.
Another, called the Thermo-electric comparative test, displays a value of electromotive force (similar to that obtained from a thermocouple), on a dial.
To get the reading, one should touch the surface of the sample, located on the instrument base plate, with a heated copper electrode.
The required ranges to be obtained are determined beforehand with known samples.
We may mention that other tests for Material-identification require more specialized knowledge and laboratory equipment, probably not readily available to most welding shops.
One of the most informative and useful for welding purposes, even more than complete chemical analysis reports, consists in metallographic examinations.
These are performed under optical microscope on specially ground, polished and etched specimens, by knowledgeable metallurgists.
For more information on issues relative to Welding for Repair see our page on Repair Welding.
Our Article on the same subject can be reached from our page on
Welding Articles.
NEW RESOURCES
Find some interesting links in a special Mid Month Bulletin Page of our PRACTICAL WELDING LETTER, designed offer you, our interested readers, the opportunity to search the web quickly and effectively on the subject of Repair Welding and related Subjects.
We urge you to explore this rich source of essential knowledge. Online Resources on Repair Welding, Failure Analysis, Material and Condition Determination, Procedure Development , presenting Articles, Downloads, Links and Information is now available by clicking on PWL#054B.
|
Looking for more Online Reference Links? Click on Welding Resources
Watch the following Video on
Handheld XRF analyser for metals https://www.youtube.com/watch?v=-0IwGLYxKnY&feature=related |
* * *
Any questions or comments or feedback? Write them down and send them to us by e-mail.
Click on the Contact Us button in the NavBar at top left of every page.
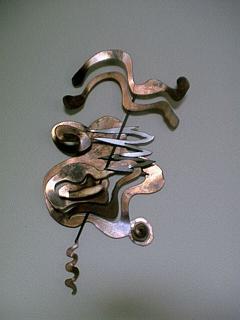
Artwork for Hobby
[From https://www.welding-advisers.com/artwork-for-hobby.html]
Let us remind you that, if you are interested, we offer a no cost subscription to our Practical Welding Letter and a bonus book in pdf format to be made available for download to your computer on the subject of
PRACTICAL HARDNESS TESTING MADE SIMPLE. Click on Subscription.
You already know how important it is to know the material condition and to understand if welding will weaken the properties or even produce cracks...
To reach a Guide to the collection of the most important Articles from Past Issues of Practical Welding Letter, click on Welding Topics.
Note: To view Google Ads, Please
Right Click and Open in a New Window.
|
Back Home
Site Map
Materials.
Metals Knowledge
Cast Iron Welding
Steel Welding
Alloy Steel Welding
Tool Steel Welding
Stainless Steel Welding
Aluminum Welding
Welding Aluminum, Reprint from HIWT
Magnesium Welding
Titanium Welding
Welding Nitinol
Copper Welding
Heat Resisting Alloys Welding
Joining Lead Tin Zinc
Refractory Metals Welding
Precious Metals Joining
Material-identification Top
We Were Just Trying to Make Ends Meet
How could you start an Online Business?
Watch the video...
Click on the following image to watch the SBI! TV Show!
POWERED BY:
Click on this Logo NOW!
Copyright (c) 2003-2008, 2009, 2010, 2011, 2012, 2013, 2014, 2015, 2016, 2017
by Elia E. Levi and www.welding-advisers.com
All Rights Reserved.
Material-identification: how to ensure basics and procedures for unknown metals even before trying to weld. Find here how to do just that...