Welding-aluminum
and Aluminum Alloys
SOLUTIONS with Effective, Powerful Advice
Welding aluminum: Discover its Easy Secrets |
Welding Problem? Solve it! with
Help from a Welding Professional Contact Us.
|
Note: To view Google Ads, Pls.
Right Click and Open in a New Window.
|
Welding-aluminum is not difficult, provided you refer to a weldable aluminum alloy once the problems are clarified.
You certainly know all you need for welding the aluminum alloys you usually work with.
What about other aluminum alloys?
Is there anything worth knowing for welding them?
What aluminum alloy type and material conditions affect weldability?
Visit the NEW Page on Welding Applications, for
selecting correctly the ways and means needed for productive performance.
Visit the NEW Page on Welding Problems,
for looking into the causes of production hindrances.
Visit the NEW Page on Architectural Metalwork,
for reviewing a few momentuous icons of excellent fabrications.
This Site is designed to cast light on the kind of problems you may meet when confronting a new Welding-aluminum job.
It might help you, in case you wonder, so that you know in advance what to do.
You could also write your problem down and send it over to us. For any questions on these subjects write us by e-mail.
Click on the Contact Us Button in the NavBar.
Welding-aluminum alloys: Heat Treatments and Weldability
Welding-aluminum is concerned with aluminum alloys weldability.
Click on Weldability Testing
This is a qualitative assessment of the material suitability to be welded by a certain process in a properly designed structure under given conditions, to present a specified quality level (that is without unacceptable defects), and to perform in service according to given requirements.
Note: To view Google Ads, Please
Right Click and Open in a New Window.
|
Therefore...
...materials like aluminum alloys may show different weldability in different conditions for different processes but may still be satisfactorily welded with particular precautions, generally spelled out in detailed procedures.
Welding-aluminum is easy for certain aluminum alloys, in that it can be done without special precautions by manual arc welding processes under most conditions to provide acceptable and consistent welds. Welding by Oxyacetylene flame with a flux, although possible, is not recommended.
It should be remembered however, that aluminum produces easily, just by sitting in air, an impervious layer of aluminum oxide which protects the surface from corrosive attacks, but also interferes with welding. Special cleaning procedures are required to remove the oxide before welding or brazing.
Aluminum oxide melts at a much higher temperature than aluminum metal.
If the oxide is not removed completely, it interferes with welding and will cause incomplete fusion.
Hydrogen dissolves rapidly in molten aluminum, but it is rejected upon cooling to form porosity. Any possible source of hydrogen (moisture, or hydrated oxides) must be removed.
Filler metal must be stored in a heated dry place to avoid that.
Electrical conductivity is about 60% of that of copper, therefore resistance heating in the torch does not occur.
This observation may need some explanation to be understood.
The torch referred to in the previous sentence is that used for Gas Metal Arc Welding (GMAW or Mig).
It is known that, when in operation, electric current flows in the coiled filler metal in the portion of wire between the contact collar and the arc, located on the workpiece.
In other materials this current, flowing along a rather short piece of wire, heats up the filler metal (preheats) quite a lot, due to the elevated value of the electrical resistance of the material in cause.
However, in aluminum, as the electrical resistance is low and the conductivity is high, this preheating effect is almost negligible.
Long contact tubes in GMAW torches for Welding-aluminum are preferred, to avoid arcing in the torch because of incomplete contact with partially oxidized filler wire.
Thermal conductivity is about 6 times that of steel. As such, heat is withdrawn rapidly from the weld pool. Therefore relatively higher heat inputs and moderate welding speeds are necessary for Welding-aluminum.
To provide steady heat input with fast processes, constant current power supplies are preferred. Alternating current (AC) can be used, except that the arc is not quite stable and the torch risks overheating.
Polarity
With AC, during the half cycle when the electrode is positive and the workpiece is negative, the electrons coming out of the workpiece break up what is left of the oxide layer: this action is known as cathodic cleaning and is essential for successful Welding-aluminum.
To avoid torch overheating new power supplies propose square wave configurations where both the time proportions of electrode positive vs. negative and the relative intensities can be finely adjusted.
The effect is a more stable arc (than with simple AC), better penetration, and a more balanced heat distribution between torch and workpiece.
Note: On heat distribution see the page on Arc Welding.
Aluminum does not change color while being heated. The welder must see the melting to be able to control the Welding-aluminum progress.
Tip!: If you are in the design stage, it is strongly recommended that, besides other things, you consider also, or ask about, the weldability of the material you help to select.
But if you are past that stage and you have to weld whatever aluminum alloy other people selected, well then the best thing you can do is to be sure it is weldable, to look for an appropriate process and a suitable procedure.
Material identification is important for Welding-aluminum in view of developing a suitable welding procedure.
Note: For information on welding characteristics of other Materials see the related pages listed in the Site Map.
For which properties is Aluminum selected?
Welding-aluminum alloys raw materials is performed on Castings, Forgings or Wrought product forms.
The properties which make these materials useful for various applications are mostly low density (specific weight), which is about one third that of steel, ease of fabrication, good thermal and electrical conductivity, pleasant appearance, corrosion resistance and also useful relative strength.
Welding-aluminum can be performed on alloys of different properties if one knows the difference.
The outstanding characteristic of aluminum is its lightness, which is put to profit in transportation, cars, boats, trains, aviation, and moving machine elements.
Some of the alloys can be hardened by special procedures of heat treatment, while others can only be strengthened by cold work and deformation.
After Welding-aluminum, it can be made impervious to atmospheric corrosion, a property which contributes to its selection for decorative and structural elements of architectural construction.
This property is promoted by applying an electrochemical process known as anodizing.
Aluminum is easily cast, forged, formed, welded (within certain limits) and finished to pleasant appearance.
Different protective coatings, like anodizing, some with special hardness, can be built integrally upon the external surfaces.
Although less than copper, aluminum is a good conductor of heat and electricity.
Aluminum scrap is valued because recycling is less energy intensive than primary production.
Aluminum alloys wrought products are listed usually, at least in the USA, according to the Aluminum Association designations, making use of a number where the first figure represents a class and the other three represent a specific type.
The temper convention defines the condition of different products: O is annealed condition. T- followed by a number indicates solution and aged condition. H- followed by a number indicates the degree of strain hardening of non heat treatable alloys. F is as fabricated.
What is the difference?...
Welding-aluminum of non heat treatable alloys (of the 1xxx, 3xxx, 5xxx, classes) is readily performed by arc processes except that if their elevated mechanical properties were obtained by mechanical work (also called strain hardening), the strength can be locally reduced by the weld heat and cannot be restored.
Welding-aluminum alloys: Heat Treatments and Weldability
Heat treatable aluminum alloys (of the 2xxx or 7xxx classes) include finely tuned proportions of certain elements (i.e. copper, zinc etc.) that through a delicate play of solutioning (by heating and rapid quenching) and precipitation out of solution in well defined procedures (either by natural aging or by heating), produce improved mechanical properties as explained in the following.
Welding-aluminum on these alloys in heat treated conditions is less favorably performed and only with special precautions or by certain processes only (Resistance welding), as briefly detailed in the following.
Heat Treatment of non weldable Aluminum Alloys
To put some order in the above and to appreciate why Welding-aluminum is not always feasible, we should first understand the structure of hardenable Aluminum Alloys. In very simple terms, Aluminum Alloys of Type 2xxx include about 5% of copper which confers special properties to the material.
It all depends on a property called solubility, that is the capacity of an element of being dissolved into another in what is called solid solution.
The favorable situation arises when at room temperature the solubility is limited, while it is larger at a more elevated temperature (less than the melting point).
When this situation arises, at the higher temperature the atoms of the less abundant element take definite positions in crystals, which are the building blocks of the alloy, but at room temperature, say after cooling from melting, they group in disorganized lumps.
With some elements, like copper in aluminum, a strange effect appears.
While heating at a certain temperature, below the melting point, all of the copper present enters into uniform solution, like sugar in water (except that we are talking here of Solid Solution).
A property called diffusion provides the driving force for displacing copper atoms into the matrix (the mass) of aluminum, so that the density of copper atoms, given sufficient time, is homogeneous or equal in each and every point.
When the material is cooled back to room temperature one of two different things may happen. If cooling is slow, copper atoms driven by the reduced solubility at lower temperature, will again group themselves in lumps, useless for providing improved properties.
But if cooling takes place immediately, by quenching the material into water, the copper atoms have no time to diffuse back, so they remain trapped in a so called supersaturated solution at room temperature, which is a not so stable condition.
Then just by themselves, in about four days, they precipitate out of solution in tiny particles or "phases", in a microstructure which exhibits much higher mechanical properties (strength and hardness). This process is called natural aging.
A similar process called artificial aging, is produced much more quickly by heating at about 120 to 180 °C (250 to 360 °F).
That is why the complete process is called solutioning and precipitation hardening.
Welding-aluminum of these types, will not only hurt the mechanical properties, but also the corrosion resistance, practically destroying the properties that made them useful in the first place: therefore they are considered non-weldable, except by resistance welding.
Tip!: If an unscrupulous subcontractor attempts to repair weld an unweldable aluminum alloy, against the rules, his mischief will most likely be detected visually after anodizing...
Other heat treatable alloys (of 6xxx class) are weldable but the properties should be restored after welding, if required, by renewed heat treatment.
Both Heat Treatable and Non Heat Treatable Aluminum Alloys in sheet form can be usually welded by Resistance Spot Welding (RSW).
An Article on Inserted strips in Resistance Spot Welding was published (3) in Issue 136 of Practical Welding Letter for December 2014.
Click on PWL#136 to see it.
Cast Aluminum Alloys can also be classified according to their specific weldability. Welding-aluminum alloy castings for repair can be done in certain cases only before hardening by heat treatment.
Find additional information on these subjects in the page on Aluminum Welding.
Dip Brazing of aluminum alloys is briefly reviewed in a related page on Brazing Heating.
See also our NEW Page on Brazing Aluminum.
Watch this Miller MIG Welders Video on |
If you did not yet find what you need, why not typing your question in the following Search Box?
An Article on brazing Aluminum to Steel explaining how two companies providing solutions to the automotive industry developed two different solutions to the problem of joining (by fusion) incompatible materials, was published in Issue No. 43 of Practical Welding Letter for March 2007 (section 4).
Click on PWL#043 to read it.
An Article on Low Porosity Laser Welding was published (11) in
Issue No. 55 of Practical Welding Letter for March 2008.
Click on PWL#055 to read it.
An Article on Resources on Filler Metals for Aluminum Welding was published (4) in Issue 58 of Practical Welding Letter for June 2008.
Click on PWL#058 to read it.
An Article presenting the new Aluminum Design Manual, 2010 Edition, was published (4) in issue 85 of Practical Welding letter for September 2010.
Click on PWL#085 to read it, and also see hereafter.
An Article on Stick Electrodes for Welding Aluminum? was published (4) in Issue 87 of Practical Welding letter for November 2010.
Click on PWL#087 to see it.
An Article on Filler Metals for Aluminum Magnesium Alloys was published (4) in Issue 101 of Practical Welding Letter for January 2012.
Click on PWL#101 to see it.
An Article on Aluminum Filler Metals for Resistance to SCC" (Stress Corrosion Cracking) was published (4) in Issue 106 of Practical Welding Letter for June 2012.
Click on PWL#106 to see it.
An Article on Filler Metals for welding Aluminum Alloy 6005-T6 was published (4) in Issue 111 of Practical Welding Letter for November 2012.
Click on PWL#111 to read it.
An Article on Filler Metal New Specification AWS A5.10:2012 was published (4) in Issue 113 of Practical Welding Letter for January 2013.
Click on PWL#113 to see it.
An Article on Aluminum Welding Safety Tips was published (3) in Issue 122 of Practical Welding Letter for October 2013.
Click on PWL#122 to see it.
An Article on Filler Metal Spec Changes was published (4) in Issue 144 of Practical Welding Letter for August 2015.
Click on PWL#144 to see it.
An introduction to a new website page on Weld-preparation and to a resource page on the same subject were published (8) in Issue 147 of Practical Welding Letter for November 2015.
Click on PWL#147.
An Article on Feedability of Aluminum Filler Metal in GMAW was published (3) in Issue 155 of Practical Welding Letter for July 2016.
Click on PWL#155.
An Article on Filler Metals for welding aluminum alloys was published (4) in Issue 163 of Practical Welding Letter for March 2017.
Click on PWL#163.
An Article on Aluminum Filler Metal Questions was published (4) in Issue 165 of Practical Welding Letter for May 2017.
Click on PWL#165.
An Article on How to Prevent Defects in arc welded Aluminum was published (7) in Issue 166 of Practical Welding Letter for June 2017.
Click on PWL#166.
An Article on Advances for Filler Metal fusing in Aluminum robotic welding was published (4) in Issue 169 of Practical Welding \Letter for September 2017.
Click on PWL#169.
To get at no cost every issue of PWL as it is published, please subscribe.
AA ADM-1
Aluminum Design Manual, 2010 Edition
Aluminum Association / 2010 /
ANSI/AWS D1.2/D1.2M:2008
Structural Welding Code - Aluminum
Edition: 5th
American Welding Society / 23-Jun-2008 / 228 pages
An Article announcing a new issue of
AWS D1.2/D1.2M:2014
- Structural Welding Code - Aluminum
was published (4) in Issue 134 of
Practical Welding Letter for October 2014.
Click on PWL#134 to see it.
ANSI/AWS A5.10/A5.10M:2012 (ISO 18273:2004 MOD)
Specification for Bare Aluminum-Alloy Welding Electrodes and Rods
American Welding Society / 04-Oct-2012 / 46 pages
NEW RESOURCES
Find some interesting links in a special Mid Month Bulletin Page of our PRACTICAL WELDING LETTER, designed to offer you, our interested readers, the opportunity to search the web quickly and effectively on the subject of welding Aluminum. We urge you to explore this rich source of essential knowledge. Online Resources on Aluminum and Aluminum Alloy Welding
, presenting Downloads, Previews, Links and Information are now available by clicking on PWL#041B and on recent Bulletin 121.
|
Looking for more Online Reference Links?
Click on Welding Resources
We discuss some of the processes applicable to Welding-aluminum and its alloys in another page, readily accessible by clicking on the underlined title, as indicated hereafter: Aluminum welding processes.
Metal Matrix Composites
An Article on Metal Matrix Composites was published (11) in Issue No. 47 of Practical Welding Letter for July 2007. Click on PWL#047 to read it.
See also our page on Joining Aluminum MMC.
* * *
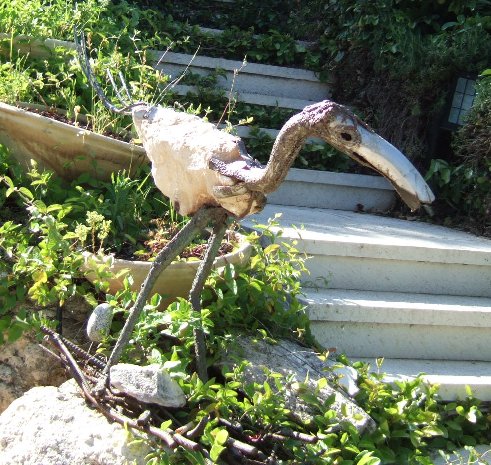
Bird by Uri Sharon
[From https://www.welding-advisers.com/Hobby-welding.html]
Any questions or comments or feedback? Write them down and send them to us by e-mail.
Click on the Contact Us button in the NavBar at top left of every page.
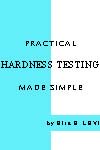
Let us remind you that you are entitled, if you are interested, to a FREE subscription to our Practical Welding Letter, that we will send to you periodically for as long as you want.
To reach a Page, listing the most important Articles from Past Issues of Practical Welding Letter, click on Welding Topics.
And also to a FREE download, right to your computer, of our book in pdf format, designed to stress important points on PRACTICAL HARDNESS TESTING MADE SIMPLE. Click here
Even if you know what Hardness Testing is all about, you might discover a few useful ideas, with direct application to your welding projects.
Note: To view Google Ads, Please
Right Click and Open in a New Window.
|
Back Home
Browse other pages at the Site Map
Metals Knowledge
Cast Iron Welding
Steel Welding
Alloy Steel Welding
Tool Steel Welding
Stainless Steel Welding
Aluminum Welding
Welding Aluminum, Reprint from HIWT
Magnesium Welding
Titanium Welding
Copper Welding
Heat Resisting Alloys Welding
Joining Lead Tin Zinc
Refractory Metals Welding
Precious Metals Joining
Welding of Plastics
For this most important subject, click on Material Identification
If you did not yet find what you need, why not typing your question in the following Search Box?
Welding-aluminum Top
Watch the following Video...
Click on the following image to watch the SBI! TV Show!
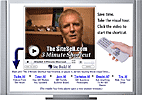
POWERED BY:
Click on this Logo NOW!
Watch - The Video:
Why Don't I Work From Home?
and also
Think outside the Cube.
Follow this Invitation!
Experience C2 power and flexibility in action by clicking SBI! 2.0 For You. Where SBIers share their business-building experiences first-hand. You will realize that there is nothing comparable to SBI! when you read real stories from SBIers who share how C2 has helped them expand, accelerate, build trust and monetize their sites.
|
Copyright (©) 2003-2010, 2011, 2012, 2013, 2014, 2015, 2016, 2017
by Elia E. Levi and www.welding-advisers.com
All Rights Reserved
Welding-aluminum and aluminum alloys: read on properties, weldability, heat treatments. Important characteristics and basic information. Follow the links...